Imagine a life where your home is a compact, sustainable haven that fits snugly within the confines of a 40-foot shipping container. Welcome to the world of shipping container tiny homes! These innovative dwellings combine affordability, eco-friendliness, and modern aesthetics. In this step-by-step guide, we’ll delve into the art of converting a shipping container into a cozy, functional abode. Whether you’re a minimalist seeking simplicity or an adventurer craving a unique living experience, this guide is your compass to navigate the exciting journey of container home conversion.
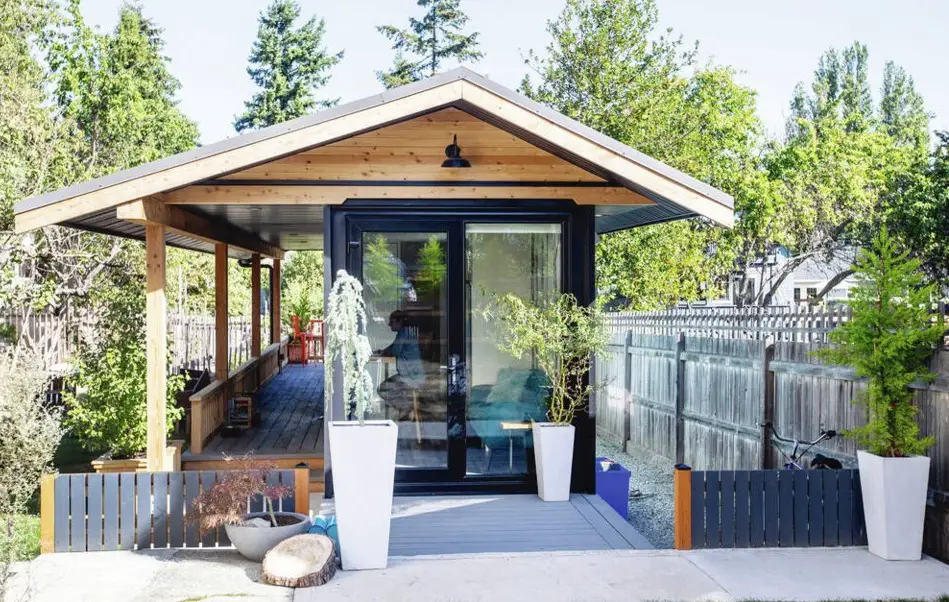
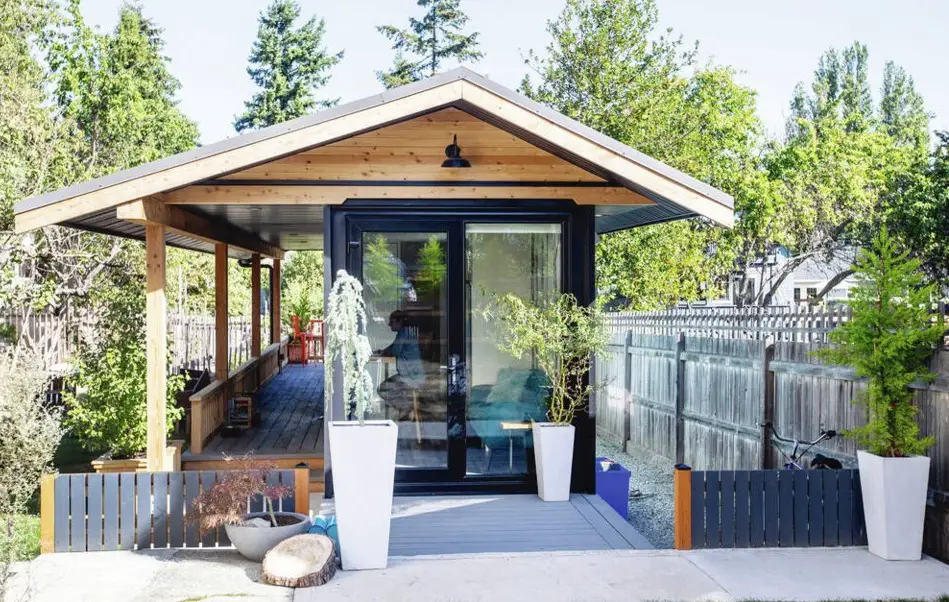
The Pros and Cons of Shipping Container Tiny Homes
Before we dive into the nitty-gritty of the conversion process, let’s weigh the pros and cons of using shipping containers as the foundation for your tiny home:
The Pros:
- Affordability: Shipping containers are budget-friendly, costing just a few thousand dollars. If you’re content with a minimalist design, your tiny home can take shape without breaking the bank.
- Environmental Consciousness: Reusing materials is a sustainable choice. However, keep in mind that transporting a massive metal box across long distances may not be the greenest option.
- Durability: Designed to withstand harsh conditions during sea voyages, shipping containers are virtually indestructible. They can brave fire, water, earthquakes, and more.
- Stackability: Planning for future expansion? Stackable container modules allow you to grow your tiny house over time.
- Aesthetic Appeal: Quirky, cool, and unconventional—shipping container homes exude a unique charm. Whether you prefer sleek modern lines or rustic industrial vibes, these structures can be customized to match your style.
The Cons:
- Insulation Challenges: Steel containers are excellent conductors of heat and cold. Proper insulation is crucial to maintain a comfortable interior temperature.
- Space Constraints: While 40 feet may seem spacious, remember that it’s still a compact living area. Clever design and efficient use of space are essential.
- Cutting and Welding Expertise Required: Transforming a container involves cutting openings for windows, doors, and utilities. Basic welding skills are beneficial.
- Permit Hurdles: Check local regulations regarding container homes. Some areas require permits, while others allow tiny homes without bureaucratic hassles.
Step-by-Step Guide: Converting Your Shipping Container
Step 1: Design Your Tiny House
- Visualize Your Space: Decide on room layouts, window placements, and overall flow. Sketch your dream tiny home.
- Plan Utilities: Determine where your kitchen, bathroom, and electrical outlets will go.
- Consider Insulation: Research insulation options suitable for your climate.
Step 2: Prepare the Container
- Choose Your Container: Opt for a 40-foot container in good condition. Inspect for rust, dents, and structural integrity.
- Clean and Treat: Remove any rust, apply anti-corrosion treatments, and repaint the exterior.
- Cut Openings: Use a plasma cutter or angle grinder to create openings for doors and windows.
Step 3: Insulate and Frame
- Insulation: Install insulation panels or spray foam to regulate temperature.
- Framing: Build wooden or metal frames for walls, ceilings, and floors.
Step 4: Install Doors and Windows
- Secure Entry Points: Install sturdy doors with proper locks.
- Natural Light: Position windows strategically for optimal sunlight and ventilation.
Step 5: Electrical and Plumbing
- Electrical Work: Wire your tiny home for lights, outlets, and appliances.
- Plumbing: Set up water supply, drainage, and a compact bathroom.
Step 6: Interior Finishes
- Flooring: Choose durable, easy-to-clean flooring materials.
- Walls: Paint or panel your walls to create a cozy ambiance.
- Kitchen and Bathroom Fixtures: Install cabinets, sinks, and fixtures.
Key Takeaways
- Creativity Rules: Embrace the challenge of working within limited space.
- Maximize Verticality: Use loft beds, storage shelves, and vertical gardens.
- Customize: Let your personality shine through in every design choice.
Conclusion
Converting a 40ft shipping container into a tiny home is an adventure that blends practicality with imagination. As you transform cold steel into warm living quarters, remember that your tiny home reflects not just your square footage but your dreams, resilience, and resourcefulness. So grab your welding mask, unleash your creativity, and embark on this remarkable journey—one container at a time.
Now, go forth and build your tiny haven—a testament to simplicity, sustainability, and the joy of unconventional living!
Check out our previous post The Cost and Availability of 40ft Shipping Containers: Navigating Global Markets