Are you looking to optimize your reverse logistics process and cut costs? Calculating your return on investment(ROI) is essential. By understanding and analyzing the financial impact of your reverse logistics operations, you can make data-driven decisions to improve efficiency and reduce expenses.
In this article, we will guide you through the steps to calculate your reverse logistics RETURN ON INVESTMENT (ROI). Whether you’re a manufacturer, retailer, or logistics service provider, these calculations are applicable to any industry. We’ll explore how to assess the costs associated with returns, repairs, and refurbishments, as well as factors like transportation, handling, and disposal.
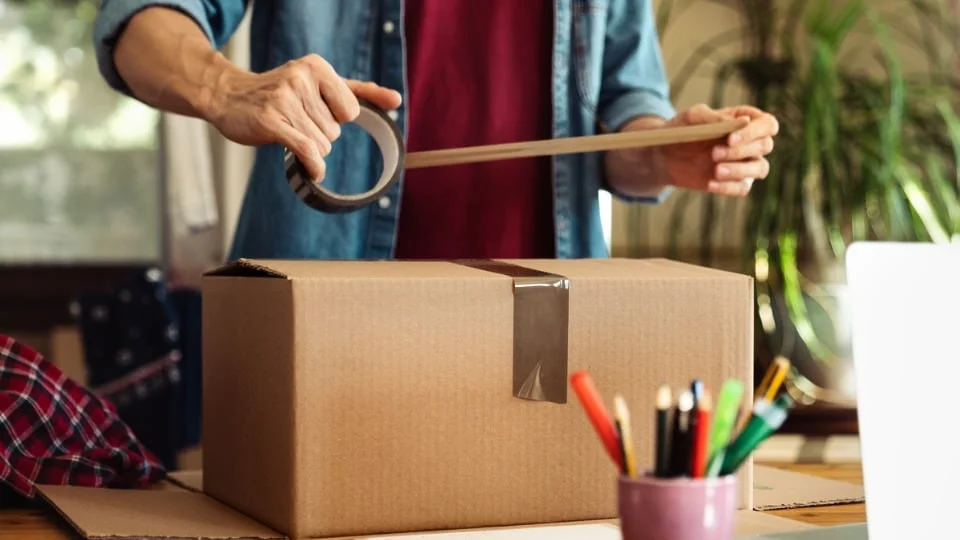
By accurately measuring your reverse logistics RETURN ON INVESTMENT (ROI), you can identify areas where unnecessary expenses occur and implement strategies to eliminate them. This helps you streamline your operations, enhance customer satisfaction, and ultimately increase your profitability.
Join us as we dive into the world of reverse logistics RETURN ON INVESTMENT (ROI) calculation and discover how you can optimize your processes and cut costs effectively.
What is reverse logistics and why is it important?
Reverse logistics refers to the process of handling returned products, repairs, and refurbishments, as well as managing their transportation, handling, and disposal. It is a critical aspect of any supply chain, as it involves managing the flow of goods in the opposite direction, from the customer back to the manufacturer or retailer.
The importance of reverse logistics lies in its ability to minimize the financial impact of product returns and repairs, as well as reduce waste and environmental impact. By efficiently managing reverse logistics, companies can recover value from returned products, optimize repair processes, and reduce overall costs. This is crucial for maintaining customer satisfaction and ensuring a sustainable and profitable business.
Understanding the concept of Return on Investment (RETURN ON INVESTMENT (ROI))
Return on Investment (RETURN ON INVESTMENT (ROI)) is a financial metric used to evaluate the profitability of an investment. It measures the return or profit generated relative to the cost of the investment. In the context of reverse logistics, calculating RETURN ON INVESTMENT (ROI) helps you assess the financial impact of your operations and determine the effectiveness of your investments in improving efficiency and reducing costs.
To calculate reverse logistics RETURN ON INVESTMENT (ROI), you need to consider both the costs and the benefits associated with your reverse logistics activities. Costs include expenses related to returns, repairs, transportation, handling, and disposal, while benefits can include recovered value from returned products, reduced repair costs, and improved customer satisfaction. By comparing the costs and benefits, you can determine whether your reverse logistics operations are generating a positive or negative return on investment.
Key factors to consider when calculating reverse logistics RETURN ON INVESTMENT (ROI)
When calculating reverse logistics RETURN ON INVESTMENT (ROI), there are several key factors you need to consider. These factors will help you ensure that your calculations are comprehensive and accurate:
1. Returns Volume: The number of products returned and the frequency of returns impact the costs associated with reverse logistics. Higher return volumes may lead to increased transportation, handling, and processing costs.
2. Returns Rate: The returns rate is the percentage of products sold that are returned. A high returns rate indicates potential issues with product quality, customer satisfaction, or other factors that need to be addressed to minimize costs.
3. Return Reasons: Understanding the reasons for returns can help identify areas for improvement. For example, if a significant number of returns are due to product defects, it may be necessary to invest in quality control measures to reduce repair and replacement costs.
4. Transportation Costs: Reverse logistics involves transporting returned products back to the appropriate facilities. Assessing transportation costs is crucial for calculating the overall cost of reverse logistics.
5. Handling and Processing Costs: The costs associated with receiving, inspecting, sorting, and processing returned products should be considered. These costs can vary depending on the complexity of the products and the required refurbishment or repair processes.
6. Disposal Costs: If returned products cannot be resold or refurbished, disposal costs need to be accounted for. Disposing of products in an environmentally friendly manner can incur additional expenses.
By considering these factors, you can ensure that your reverse logistics RETURN ON INVESTMENT (ROI) calculations accurately reflect the costs and benefits associated with your operations.
Steps to calculate your reverse logistics RETURN ON INVESTMENT (ROI)
Calculating reverse logistics RETURN ON INVESTMENT (ROI) involves several steps that help you analyze the financial impact of your operations and determine the effectiveness of your investments. Here’s a step-by-step guide to help you through the process:
1. Gather Data: Collect all relevant data, including returns volume, return reasons, transportation costs, handling and processing costs, and disposal costs. Ensure that the data is accurate and up-to-date.
2. Calculate Costs: Calculate the total costs associated with your reverse logistics operations. This includes transportation costs, handling and processing costs, and disposal costs. Consider both direct costs (e.g., labor, transportation fees) and indirect costs (e.g., lost sales, customer dissatisfaction).
3. Assess Benefits: Determine the benefits generated by your reverse logistics operations. This includes recovered value from returned products, reduced repair costs, and improved customer satisfaction. Assign monetary values to these benefits based on market prices, repair costs, and customer feedback.
4. Calculate RETURN ON INVESTMENT (ROI): Subtract the total costs from the total benefits to calculate the net return. Divide the net return by the total costs and multiply by 100 to calculate the RETURN ON INVESTMENT (ROI) percentage. A positive RETURN ON INVESTMENT (ROI) indicates that your reverse logistics operations are generating more value than they cost, while a negative RETURN ON INVESTMENT (ROI) suggests that adjustments are needed to improve efficiency and reduce costs.
5. Analyze Results: Evaluate the RETURN ON INVESTMENT (ROI) percentage to assess the overall profitability of your reverse logistics operations. Identify areas where costs are high or benefits are low to determine potential cost-saving opportunities.
6. Iterate and Improve: Use the insights gained from the RETURN ON INVESTMENT (ROI) calculation to implement strategies and improvements that reduce costs and increase efficiency. Regularly monitor and recalculate the RETURN ON INVESTMENT (ROI) to track progress and ensure ongoing optimization.
By following these steps, you can gain valuable insights into the financial impact of your reverse logistics operations and make informed decisions to improve efficiency and reduce costs.
Identifying cost-cutting opportunities in reverse logistics
To optimize your reverse logistics operations and cut costs effectively, you need to identify areas where unnecessary expenses occur. Here are some key cost-cutting opportunities to consider:
1. Product Quality Improvement: Investing in product quality improvement can reduce the number of returns due to defects or malfunctions. By ensuring that products meet or exceed customer expectations, you can minimize repair and replacement costs.
2. Streamlined Return Processes: Simplify and streamline your return processes to reduce handling and processing costs. Implement efficient return authorization systems, automate return documentation, and optimize the flow of returned products through your facilities.
3. Inventory Management: Optimize inventory management to minimize the quantity of returned products held in stock. Implement systems that accurately track and forecast product demand, allowing you to reduce the costs associated with excess inventory and obsolescence.
4. Transportation Optimization: Explore transportation optimization strategies to reduce transportation costs. Consolidate shipments, use efficient routes, and negotiate favorable rates with carriers to minimize expenses.
5. Refurbishment and Repair Efficiency: Improve the efficiency of refurbishment and repair processes to reduce labor and material costs. Implement standardized processes, train employees, and leverage technology to streamline these operations.
6. Customer Communication and Education: Enhance customer communication and education to minimize preventable returns. Provide detailed product information, clear instructions, and proactive customer support to help customers make informed purchasing decisions and reduce the likelihood of returns.
By identifying and implementing these cost-cutting opportunities, you can significantly reduce expenses in your reverse logistics operations and improve your overall profitability.
Strategies to reduce costs in reverse logistics
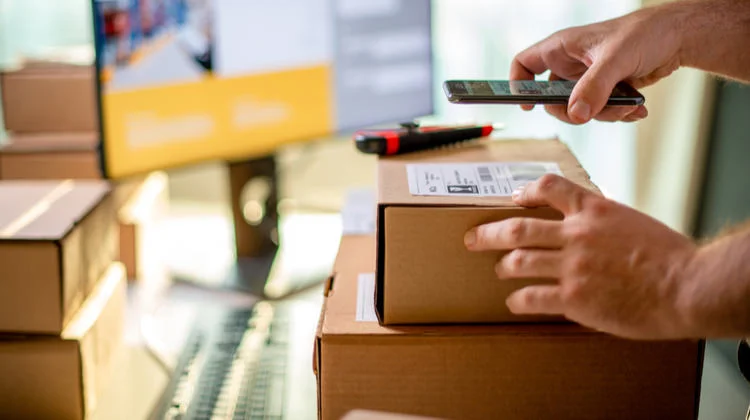
In addition to identifying specific cost-cutting opportunities, there are several strategies you can implement to reduce costs in reverse logistics:
1. Optimize Reverse Supply Chain: Streamline the reverse supply chain by integrating it with the forward supply chain. This allows for better visibility and coordination, reducing transportation and handling costs.
2. Collaborate with Partners: Collaborate with manufacturers, retailers, and logistics service providers to share resources and reduce costs. For example, sharing return centers or transportation networks can lead to significant cost savings.
3. Implement Lean Principles: Apply lean principles to reverse logistics operations to eliminate waste and improve efficiency. This includes reducing unnecessary movement, inventory, waiting time, and defects.
4. Invest in Technology: Leverage technology solutions such as barcode scanning, RFID tracking, and data analytics to improve visibility, accuracy, and efficiency in reverse logistics processes. Automation and digitization can significantly reduce costs and enhance overall performance.
5. Continuous Improvement: Establish a culture of continuous improvement by regularly evaluating and optimizing reverse logistics processes. Encourage employee input, monitor key performance indicators, and implement feedback loops to drive ongoing cost reductions.
By adopting these strategies, you can create a lean and efficient reverse logistics operation that minimizes costs and maximizes value.
Best practices for optimizing reverse logistics processes
To optimize your reverse logistics processes and achieve maximum cost savings, consider the following best practices:
1. Data Analysis: Utilize data analytics to gain insights into return patterns, customer behavior, and areas for improvement. Leverage this data to make informed decisions and drive continuous optimization.
2. Collaboration: Foster collaboration among stakeholders, including manufacturers, retailers, customers, and logistics partners. By working together, you can identify and address inefficiencies and reduce costs throughout the reverse logistics process.
3. Invest in Training: Provide comprehensive training for employees involved in reverse logistics processes. This ensures that they have the necessary skills and knowledge to handle returned products efficiently and effectively.
4. Customer Feedback: Gather and analyze customer feedback to identify areas for improvement in product quality, packaging, and instructions. Use this feedback to drive product and process enhancements that reduce returns and associated costs.
5. Reverse Logistics Network Optimization: Optimize your reverse logistics network by strategically locating return centers, repair facilities, and disposal sites. This minimizes transportation costs and reduces the time required to process returns.
By implementing these best practices, you can optimize your reverse logistics processes and achieve significant cost savings.
Case studies of companies successfully cutting costs in reverse logistics
To illustrate the effectiveness of cost-cutting strategies in reverse logistics, let’s explore two case studies of companies that have successfully reduced costs:
1. Case Study in a Packaging Industry: This study maps the reverse logistics of an industrial packaging company in northern Santa Catarina, Brazil. The company implemented measures to mitigate the environmental impacts generated by the production process. They focused on the correct disposal of waste produced by the company, making the reverse flow of the products for their recycling increasingly important. From the knowledge of the costs involved in this reverse flow, the company was able to better understand this process and implement improvements to reduce waste. The study found that reverse logistics can generate positive revenue for the company, besides generating environmental and social gains.
2. Economic Order Quantity (EOQ) Model with Environmental and Social Considerations: This study incorporated sustainable costs in reverse logistics processes using the Economic Order Quantity (EOQ) model. The model was extended for lot-sizing in reverse logistics that considers environmental, social, and economic parameters. The study found that carbon prices have a significant impact on the remanufacturing tax, i.e., the proportion of reusable items in a reverse supply chain that are successfully remanufactured. Additionally, it was noted that high social costs, calculated as a function of ergonomic conditions, can invalidate a high remanufacturing tax. As a consequence, poorly planned labor conditions in reverse logistics can lead to lower recycling rates due to inefficient use of social resources.
These case studies demonstrate that effective cost-cutting strategies in reverse logistics not only reduce costs but also contribute to sustainability and social responsibility.
Tools and software for tracking and analyzing RETURN ON INVESTMENT (ROI)
To effectively track and analyze your reverse logistics RETURN ON INVESTMENT (ROI), consider leveraging the following tools and software:
1. Reverse Logistics Management Systems: These systems provide end-to-end visibility and control over reverse logistics operations. They track returns, manage repair processes, and generate reports that help analyze costs and measure RETURN ON INVESTMENT (ROI).
2. Data Analytics Platforms: Data analytics platforms enable you to collect, analyze, and visualize data related to reverse logistics. They provide insights into return patterns, customer behavior, and cost-saving opportunities.
3. Transportation Management Systems: Transportation management systems optimize transportation routes, consolidate shipments, and provide real-time visibility into transportation costs. They help reduce transportation expenses in reverse logistics.
4. Inventory Management Systems: Inventory management systems help optimize inventory levels, reduce holding costs, and prevent excess stock in reverse logistics. They provide accurate demand forecasting and improve inventory turnover.
5. Customer Relationship Management (CRM) Systems: CRM systems help gather and analyze customer feedback, track returns, and identify areas for improvement. They provide insights into customer satisfaction and help drive product and process enhancements.
By leveraging these tools and software, you can streamline your reverse logistics operations, improve data analysis capabilities, and effectively measure your RETURN ON INVESTMENT (ROI).
Conclusion and next steps for implementing cost-saving measures in reverse logistics
Calculating your reverse logistics RETURN ON INVESTMENT (ROI) is crucial for optimizing your processes and cutting costs effectively. By understanding the concept of RETURN ON INVESTMENT (ROI), considering key factors, and following the steps outlined in this article, you can gain valuable insights into the financial impact of your operations.
Identifying cost-cutting opportunities, implementing strategies to reduce costs, and adopting best practices will help you achieve significant savings in your reverse logistics operations. Additionally, learning from case studies and utilizing tools and software will enhance your ability to track and analyze your RETURN ON INVESTMENT (ROI).
Take the next step and begin implementing cost-saving measures in your reverse logistics operations. Start by assessing your current processes, identifying areas for improvement, and developing an action plan. Regularly monitor your RETURN ON INVESTMENT (ROI) and adjust your strategies as needed to ensure ongoing optimization.
By focusing on optimizing your reverse logistics RETURN ON INVESTMENT (ROI), you can streamline your operations, enhance customer satisfaction, and ultimately increase your profitability.
FAQs
1. Reverse logistics ROI is a critical metric for evaluating the financial impact of your reverse logistics operations. It helps you assess the effectiveness of your investment in managing product returns and optimizing cost savings.
2. To calculate reverse logistics ROI, you need to consider both the financial gains and the costs associated with your return processes. Financial gains can include savings from reduced product returns, improved asset recovery, and increased customer satisfaction. Costs can include transportation, processing, refurbishment, and disposal expenses.
3. Start by identifying and quantifying the financial gains resulting from your reverse logistics efforts. This can be achieved by analyzing data on reduced return rates, improved product resale value, and higher customer retention rates.
4. Next, calculate the costs associated with reverse logistics. This includes transportation costs for returned products, labor costs for processing and refurbishment, warehousing expenses, and disposal costs for unsalvageable items.
5. Once you have the financial gains and costs, use the following formula to calculate the reverse logistics ROI: ROI = (Financial Gains – Costs) / Costs * 100. This will give you a percentage that represents the return on your investment in reverse logistics.
6. Cutting costs in reverse logistics can be achieved through various strategies. Some effective approaches include optimizing transportation routes, streamlining processing and refurbishment procedures, implementing automation and technology solutions, and collaborating with reliable partners and service providers.
7. Continuous monitoring and analysis of reverse logistics data are crucial for identifying areas of improvement and cost-saving opportunities. Leverage analytics tools and software to track key metrics, such as return rates, processing time, and disposal costs, to identify trends and make data-driven decisions.
8. Remember that reverse logistics ROI is not a one-time calculation. It should be regularly reassessed to track the performance of your reverse logistics operations and identify areas for further optimization.
9. By calculating reverse logistics ROI and implementing cost-cutting measures, businesses can improve their bottom line, enhance customer satisfaction, and contribute to sustainability by reducing waste and maximizing asset recovery.
10. As reverse logistics becomes increasingly important in today’s business landscape, organizations that effectively calculate ROI and cut costs will gain a competitive advantage by optimizing their operations and profitability.
Check out our previous blog post by clicking here: