Key takeaways: Reverse Logistics
- Efficient reverse logistics processes reduce costs and improve customer satisfaction.
- Key activities include returns management, inspection and sorting, repairs and refurbishment, inventory management, and disposal and recycling.
- Properly managed reverse logistics contribute to environmental sustainability by promoting recycling and reducing waste.
- Positive returns experiences increase customer retention and encourage repeat purchases.
- Optimized reverse logistics enhance overall supply chain efficiency and visibility.
Reverse Logistics
In today’s fast-paced world, businesses are constantly striving to improve their supply chain management processes. One crucial aspect of this is reverse logistics, which involves the flow of goods and materials from the end-user back to the manufacturer or retailer. Understanding the key activities involved in reverse logistics processes is essential for businesses to optimize their operations and maximize customer satisfaction. In this blog post, we will delve deeper into the various activities that make up reverse logistics and explore how they contribute to sustainable and efficient supply chain management.
1. Returns Management:
Returns management is the foundation of reverse logistics processes. It involves the coordination and processing of customer returns, which can range from damaged or defective products to customer dissatisfaction. Efficient returns management systems are crucial to ensure timely and accurate processing of returns, which can help businesses reduce costs and improve customer experience.
2. Inspection and Sorting:
Once the returned products are received, they undergo a thorough inspection and sorting process. This step involves assessing the condition of the returned items to determine if they can be resold, refurbished, or if they require disposal. Sorting the items based on their condition enables businesses to make informed decisions about the next steps in the reverse logistics process.
3. Repairs and Refurbishment
If a returned item is identified as repairable or refurbishable, it undergoes a repair and refurbishment process. Skilled technicians examine and fix any issues, ensuring that the product meets quality standards and is ready for resale. Repairing and refurbishing products not only reduces waste but also allows businesses to recapture value from returned items.
4. Inventory Management:
Proper inventory management is crucial in reverse logistics processes. Businesses need to keep track of the returned items, their condition, and their location within the supply chain. This helps in efficiently managing stock levels, reducing the chances of stockouts or overstocking, and ensuring that returned items are available for resale or further processing.
5. Disposal and Recycling:
For items that cannot be repaired or refurbished, proper disposal or recycling is essential. This involves adhering to environmental regulations and disposing of items responsibly. Recycling materials from returned products not only reduces waste but also promotes sustainability and resource conservation.
6. Remarketing and Resale:
Once repaired, refurbished, or sorted for resale, returned items can be reintroduced into the market. Remarketing and resale activities involve identifying suitable sales channels, pricing strategies, and marketing campaigns for the refurbished products. This step helps businesses recover value from returned items and minimize losses.
The impact of reverse logistics is significant and can have both financial and environmental benefits for businesses. Here are some key points to consider:
1. Financial Benefits:
– Optimized reverse logistics processes can save businesses money by reducing costs associated with returns, repairs, and disposal.
– Efficient returns management systems help retain customers and improve customer satisfaction, leading to increased sales and repeat purchases.
– Well-executed reverse logistics can provide valuable product data collected from customer interactions, which can be used to improve future product offerings and customer experiences.
– Best-in-class reverse logistics practices have been shown to result in 12% better customer satisfaction compared to competitors.
2. Environmental Benefits:
– Reverse logistics contributes to sustainability efforts by reducing waste and promoting recycling and refurbishment.
– Implementing sustainable practices in reverse logistics, such as using environmentally friendly packaging and reducing transportation emissions, can help companies reduce their environmental impact.
– Proper management of returned products ensures compliance with environmental regulations and helps companies avoid legal penalties.
– By extending the life cycle of products through repairs, refurbishment, and resale, reverse logistics reduces the need for new production and conserves resources.
3. Customer Satisfaction and Retention:
– A hassle-free returns process increases customer satisfaction and retention rates.
– According to a survey, 95% of customers say they will not buy again from a company if they have a bad returns experience.
– Positive returns management experiences can lead to repeat purchases, while negative experiences can drive customers away from a company permanently.
4. Supply Chain Optimization:
– Reverse logistics is an important aspect of supply chain management, allowing businesses to execute operations efficiently and increase value for their end customers.
– Proper management of returned products helps businesses maintain visibility into their inventory and make informed decisions about stock levels.
– Reverse logistics processes utilize similar technologies and systems as forward logistics, including barcodes, scanners, and electronic data interchange (EDI).
In conclusion, reverse logistics has a significant impact on businesses, offering financial benefits, environmental sustainability, improved customer satisfaction, and optimized supply chain management. By implementing efficient reverse logistics processes, businesses can reduce costs, increase customer loyalty, and contribute to a more sustainable future.

What are the key reverse logistics activities?
The key activities involved in reverse logistics can vary depending on the specific industry and company. However, here are some common activities that are typically part of reverse logistics processes:
1. Returns Management: This involves managing the return of products from customers, including handling customer inquiries, issuing return authorizations, and coordinating the physical return of the products.
2. Inspection and Sorting: Once returned products are received, they undergo inspection to assess their condition. This step helps determine if the products can be resold, refurbished, or if they require disposal. Sorting the items based on their condition is essential for making informed decisions about the next steps in the reverse logistics process.
3. Repairs and Refurbishment: If returned items are identified as repairable or refurbishable, they undergo repair and refurbishment processes. Skilled technicians examine and fix any issues, ensuring that the products meet quality standards and are ready for resale.
4. Inventory Management: Proper inventory management is crucial in reverse logistics processes. It involves tracking returned items, their condition, and their location within the supply chain. This helps businesses efficiently manage stock levels and ensure that returned items are available for resale or further processing.
5. Disposal and Recycling: For items that cannot be repaired or refurbished, proper disposal or recycling is necessary. This involves adhering to environmental regulations and disposing of items responsibly. Recycling materials from returned products reduces waste and promotes sustainability.
6. Remarketing and Resale: Once repaired, refurbished, or sorted for resale, returned items can be reintroduced into the market. Remarketing and resale activities involve identifying suitable sales channels, pricing strategies, and marketing campaigns for the refurbished products.
It’s important to note that reverse logistics is not limited to these activities alone. It can also include other processes such as gatekeeping, returns avoidance, packaging, unsold goods management, leases, repairs, and product retirement, depending on the specific industry and company.
Remember, reverse logistics is a dynamic field, and companies may have unique processes tailored to their specific needs and goals.
What are the processes involved in reverse logistics?
The processes involved in reverse logistics can vary depending on the industry and company. However, here are some common processes that are typically part of reverse logistics:
1. Returns Management: This process involves managing the return of products from customers, including handling customer inquiries, issuing return authorizations, and coordinating the physical return of the products.
2. Inspection and Sorting: Once returned products are received, they undergo inspection to assess their condition. This step helps determine if the products can be resold, refurbished, or if they require disposal. Sorting the items based on their condition is essential for making informed decisions about the next steps in the reverse logistics process.
3. Repairs and Refurbishment: If returned items are identified as repairable or refurbishable, they undergo repair and refurbishment processes. Skilled technicians examine and fix any issues, ensuring that the products meet quality standards and are ready for resale.
4. Inventory Management: Proper inventory management is crucial in reverse logistics processes. It involves tracking returned items, their condition, and their location within the supply chain. This helps businesses efficiently manage stock levels and ensure that returned items are available for resale or further processing.
5. Disposal and Recycling: For items that cannot be repaired or refurbished, proper disposal or recycling is necessary. This involves adhering to environmental regulations and disposing of items responsibly. Recycling materials from returned products reduces waste and promotes sustainability.
6. Remarketing and Resale: Once repaired, refurbished, or sorted for resale, returned items can be reintroduced into the market. Remarketing and resale activities involve identifying suitable sales channels, pricing strategies, and marketing campaigns for the refurbished products.
It’s important to note that reverse logistics is not limited to these processes alone. It can also include other activities such as gatekeeping, returns avoidance, packaging, unsold goods management, leases, repairs, and product retirement, depending on the specific industry and company.
Remember, reverse logistics processes can vary, and companies may have unique processes tailored to their specific needs and goals.
What are the key activities involved in logistics management?
The processes involved in reverse logistics can vary depending on the industry and company. However, here are some common processes that are typically part of reverse logistics:
1. Returns Management: This process involves managing the return of products from customers, including handling customer inquiries, issuing return authorizations, and coordinating the physical return of the products.
2. Inspection and Sorting: Once returned products are received, they undergo inspection to assess their condition. This step helps determine if the products can be resold, refurbished, or if they require disposal. Sorting the items based on their condition is essential for making informed decisions about the next steps in the reverse logistics process.
3. Repairs and Refurbishment: If returned items are identified as repairable or refurbishable, they undergo repair and refurbishment processes. Skilled technicians examine and fix any issues, ensuring that the products meet quality standards and are ready for resale.
4. Inventory Management: Proper inventory management is crucial in reverse logistics processes. It involves tracking returned items, their condition, and their location within the supply chain. This helps businesses efficiently manage stock levels and ensure that returned items are available for resale or further processing.
5. Disposal and Recycling: For items that cannot be repaired or refurbished, proper disposal or recycling is necessary. This involves adhering to environmental regulations and disposing of items responsibly. Recycling materials from returned products reduces waste and promotes sustainability.
6. Remarketing and Resale: Once repaired, refurbished, or sorted for resale, returned items can be reintroduced into the market. Remarketing and resale activities involve identifying suitable sales channels, pricing strategies, and marketing campaigns for the refurbished products.
It’s important to note that reverse logistics is not limited to these processes alone. It can also include other activities such as gatekeeping, returns avoidance, packaging, unsold goods management, leases, repairs, and product retirement, depending on the specific industry and company.
Remember, reverse logistics processes can vary, and companies may have unique processes tailored to their specific needs and goals.
Which of the following activities are key parts of logistics?
Based on the search results, the key activities of logistics can be summarized as follows:
1. Order Processing: This involves managing and processing customer orders, including order entry, verification, and documentation.
2. Inventory Management: This includes activities related to managing and controlling inventory levels, such as stock monitoring, replenishment, and optimization.
3. Freight Transportation: This refers to the movement of goods from one location to another, including activities such as transportation planning, carrier selection, and shipment tracking.
4. Storage and Warehousing: This involves the management of storage facilities and the organization of goods within warehouses, including receiving, storing, and picking items for shipment.
5. Returns Management: This process deals with the management of returned products, including handling customer inquiries, issuing return authorizations, and coordinating the physical return of the products.
6. Packaging and Unitization: Packaging plays a crucial role in logistics by ensuring the safe and efficient transportation of goods. Unitization involves grouping products together to facilitate storage and transportation.
7. Information and Controls: This includes activities related to managing information flows, such as demand forecasting, inventory control, and designing information systems to control operational procedures.
It’s important to note that logistics activities can vary depending on the industry and company. Different sources may provide slightly different perspectives on the key activities of logistics, but the activities mentioned above are commonly recognized as integral parts of logistics processes.
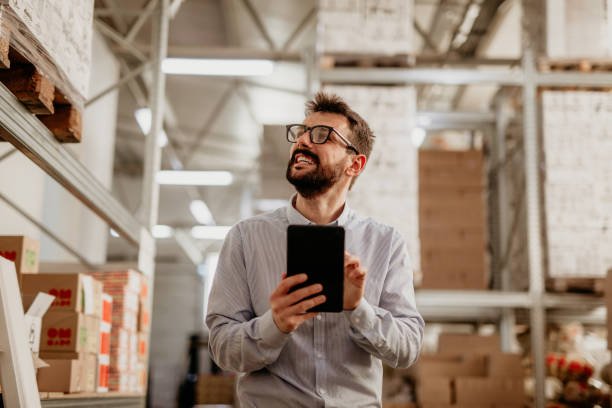
Reverse logistics is an integral part of supply chain management, and understanding the key activities involved in these processes is crucial for businesses aiming to optimize their operations. Effective returns management, inspection and sorting, repairs and refurbishment, inventory management, disposal and recycling, and remarketing and resale are all essential components of reverse logistics. By implementing efficient reverse logistics processes, businesses can reduce costs, improve customer satisfaction, and contribute to a more sustainable future. So, take the necessary steps to understand and optimize your reverse logistics activities, and watch your supply chain thrive.
Hope this article was for more check out our previous blog post by clicking here