Key takeaways
Understanding the significance of reverse logistics in supply chain management, putting into practice practical strategies like improving communication and creating clear processes, utilizing technology to streamline procedures, effectively handling returns and exchanges, and tracking performance for ongoing improvement are some of the key lessons learned from successful reverse logistics management. Businesses may optimize their reverse logistics operations, lower costs, boost customer happiness, and encourage supply chain sustainability by giving priority to five essential components. Reverse logistics management procedures will become more effective and efficient in the end if these lessons are adopted.
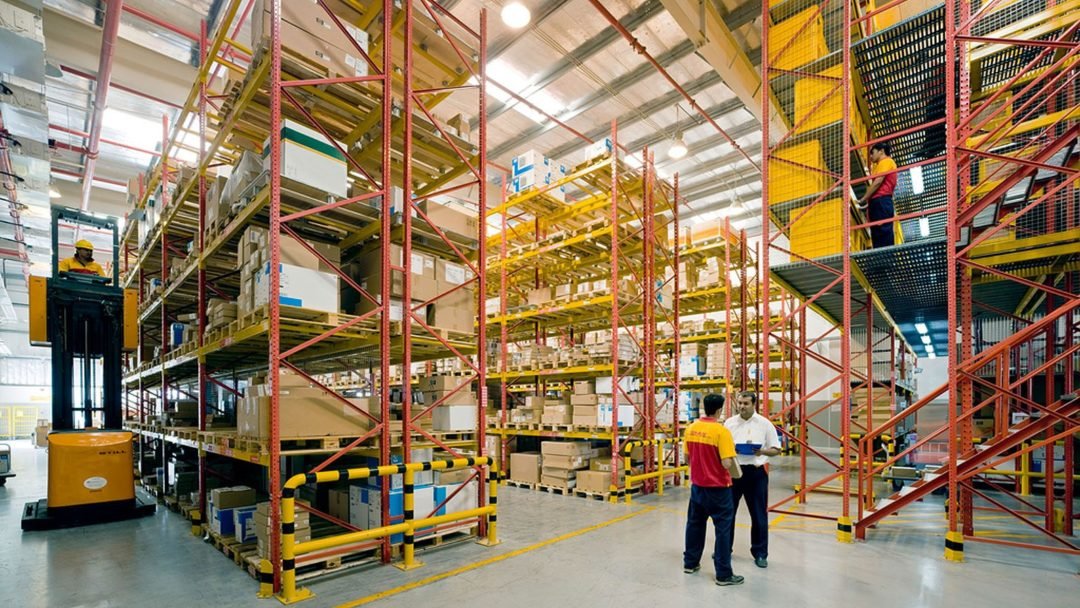
Introduction
One important but sometimes disregarded aspect of supply chain operations is reverse logistics management. Gaining an appreciation for reverse logistics may result in considerable financial savings as well as increased customer satisfaction. Through the use of successful tactics like improved communication and clear protocols, firms may decrease losses from returned items and streamline their operations. In the digital world of today, utilizing technology to optimize procedures is crucial for better accuracy and real-time visibility. Optimizing reverse logistics requires effective management of exchanges and returns. Procedures like timely processing of returns and transparent return procedures improve customer satisfaction. To ensure overall efficiency and identify areas for improvement, reverse logistics procedures must be continually improved through measurement. Businesses may prioritize these essential components to enhance their reverse logistics management practices and ultimately improve their bottom line.
Understanding the Importance of Reverse Logistics
Not only is reverse logistics a small but crucial part of supply chain management that has the power to make or ruin a company’s operations. This complex procedure ensures that items move smoothly from the point of consumption back to their origin by handling product returns, repairs, recycling, and disposal with efficiency. Businesses may greatly improve customer happiness and simplify their supply chain by comprehending and giving reverse logistics top priority.
Businesses need to understand the value that effective reverse logistics can provide in the highly competitive market of today. It involves more than just managing returns; it also involves optimizing cost savings, avoiding losses, and recovering value from returned goods. Robust reverse logistics protocols have the potential to enable organizations to turn perceived setbacks into successes. Additionally, corporations may help create a greener, more environmentally conscious future by encouraging sustainability through appropriate recycling and disposal procedures.
Furthermore, it is impossible to overestimate the influence of reverse logistics on customer satisfaction. Having easy return policies and effective product handling procedures may help firms stand out from the competition in a world where the customer experience is everything. Consumers value hassle-free returns and exchanges, and companies may cultivate a favorable reputation, trust, and loyalty among their clients by placing a high priority on reverse logistics management.
Reverse logistics is essentially the foundation of an efficient supply chain. Companies may utilize it to recover value, reduce waste, boost sustainability, and—above all—improve customer pleasure. Businesses may improve operations and prosper in a more competitive market by realizing the importance of reverse logistics and putting good plans into place.
Reverse logistics is crucial because it enables companies to recoup value from returned goods, which is one of its main benefits. Businesses may reduce losses and increase the possibility of cost savings by putting effective reverse logistics procedures in place. Additionally, by making it easier for things to be recycled or disposed of properly, reverse logistics contributes to sustainability and waste reduction.
The effect reverse logistics has on customer satisfaction is a further crucial factor. Customers appreciate companies who have easy return policies and efficiently manage exchanges or returns of merchandise. Reverse logistics management is something that companies may prioritize to improve their reputation and increase client loyalty.
In short, effective supply chain management requires a grasp of reverse logistics. It helps companies to increase customer happiness, cut waste, promote sustainability, and recoup value from returned goods.
Implementing Effective Reverse Logistics Strategies
Implementing effective reverse logistics strategies is crucial for businesses to efficiently handle product returns and exchanges, ultimately enhancing customer satisfaction and driving success in supply chain management. Here are some key strategies to consider when developing a comprehensive reverse logistics plan:
– Implement a seamless reverse logistics process: Developing a clear and well-defined process for handling returns, including establishing return policies, creating return authorization procedures, and implementing efficient product inspection and testing protocols, is essential for streamlining operations and ensuring consistency in handling returned products.
– Foster communication and collaboration: Effective reverse logistics management requires collaboration between different departments and stakeholders, such as customer service, warehouse operations, and suppliers. By enhancing communication channels and building strong relationships with partners, businesses can expedite the process of returns and exchanges.
– Utilize technology solutions: Leveraging technology tools like barcode scanning, RFID tracking, and automated data management systems can significantly improve the efficiency and accuracy of reverse logistics processes. These solutions provide real-time visibility of returned products, reducing manual errors and enhancing inventory management.
By focusing on these key strategies, businesses can streamline their operations, reduce costs, and ultimately improve overall customer satisfaction.
– Develop a clear and well-defined reverse logistics process: Having a well-defined process helps to streamline operations and ensure consistent handling of returned products. This includes establishing return policies, creating return authorization procedures, and implementing efficient product inspection and testing protocols.
– Enhance communication and collaboration: Effective reverse logistics requires collaboration between different departments and stakeholders, including customer service, warehouse operations, and suppliers. By improving communication channels and establishing strong relationships with partners, businesses can expedite the process of returns and exchanges.
– Invest in technology: Leveraging technology solutions, such as barcode scanning, RFID tracking, and automated data management systems, can greatly improve the efficiency and accuracy of reverse logistics processes. These tools enable real-time visibility of returned products, reduce manual errors, and enhance inventory management.
By implementing these effective reverse logistics strategies, businesses can streamline their operations, reduce costs, and improve overall customer satisfaction.
Leveraging Technology for Streamlined Processes
In today’s digital age, leveraging technology is crucial for streamlining reverse logistics processes. Here are some ways technology can help optimize reverse logistics management:
– Automated data management: Implementing automated data management systems can eliminate manual data entry and reduce the risk of errors. These systems can track and record important information about returned products, such as reason for return, condition, and customer details.
– Real-time visibility: Technology solutions, such as barcode scanning and RFID tracking, provide real-time visibility of returned products throughout the reverse logistics process. This enables businesses to quickly identify bottlenecks, track the status of returns, and make informed decisions to improve efficiency.
– Integration with other systems: Integrating reverse logistics systems with other supply chain management systems, such as inventory management and order fulfillment, can streamline operations and enhance overall efficiency. This integration allows for seamless data sharing and coordination between different processes.
By leveraging technology for streamlined processes, businesses can improve the accuracy, speed, and efficiency of their reverse logistics operations.
Managing Returns and Exchanges Efficiently
Efficiently managing returns and exchanges is crucial for successful reverse logistics management. Here are some key practices to consider:
– Clearly communicate return policies: Providing clear and concise return policies to customers helps set expectations and minimize confusion. This includes specifying timeframes for returns, acceptable condition of products, and any associated fees or restocking charges.
– Simplify the return process: Streamlining the return process can help reduce customer frustration and improve overall satisfaction. This can be achieved by providing pre-paid return labels, offering multiple return options (e.g., in-store, online), and simplifying the paperwork required for returns.
– Promptly process returns: Timely processing of returns is essential for improving customer satisfaction and minimizing inventory holding costs. Implementing efficient product inspection and testing procedures, as well as automating return processing workflows, can help expedite the returns process.
By managing returns and exchanges efficiently, businesses can minimize costs, enhance customer experience, and optimize their reverse logistics operations.
Measuring Performance and Continuous Improvement
Measuring the performance of reverse logistics processes is vital for identifying areas of improvement and optimizing efficiency. Here are some key steps to consider:
– Define key performance indicators (KPIs): Establishing KPIs specific to reverse logistics, such as return rate, processing time, customer satisfaction, and environmental impact, allows businesses to measure their performance comprehensively and identify opportunities for enhancement.
– Regularly analyze data: Collecting and analyzing data related to reverse logistics processes can provide valuable insights into inefficiencies and bottlenecks. By examining trends, identifying patterns, and pinpointing root causes of returns, businesses can make informed decisions to streamline operations and improve overall performance.
– Implement continuous improvement initiatives: Based on the analysis of performance data, businesses should proactively implement continuous improvement initiatives to optimize their reverse logistics processes. This may involve adjusting policies, refining procedures, or upgrading technology systems to address identified issues and drive efficiency.
By prioritizing the measurement of performance and committing to continuous improvement, businesses can not only enhance efficiency and reduce costs but also elevate customer satisfaction and sustainability efforts in their reverse logistics operations.
– Define key performance indicators (KPIs): Establishing KPIs specific to reverse logistics, such as return rate, processing time, and customer satisfaction, allows businesses to measure their performance and identify areas for improvement.
– Regularly analyze data: Collecting and analyzing data related to reverse logistics processes can provide valuable insights into inefficiencies and bottlenecks. This data can help identify patterns, pinpoint root causes of returns, and guide decision-making for process improvements.
– Implement continuous improvement initiatives: Based on the analysis of performance data, businesses should implement continuous improvement initiatives to optimize their reverse logistics processes. This can involve making changes to policies, procedures, or technology systems to address identified issues.
By measuring performance and continuously improving reverse logistics processes, businesses can enhance efficiency, reduce costs, and provide better customer service.
In conclusion, embracing the importance of reverse logistics management and implementing effective strategies is essential for optimizing supply chain operations. By understanding the significance of reverse logistics, businesses can recover value from returned products, reduce waste, and improve customer satisfaction. Developing clear processes, enhancing communication, leveraging technology, and efficiently managing returns and exchanges are key elements in streamlining reverse logistics operations. Measuring performance and continuously improving processes through the analysis of data and implementation of improvement initiatives are vital for achieving efficiency and cost savings. By prioritizing these aspects, businesses can enhance their reverse logistics management practices and ultimately drive success in their supply chain operations.
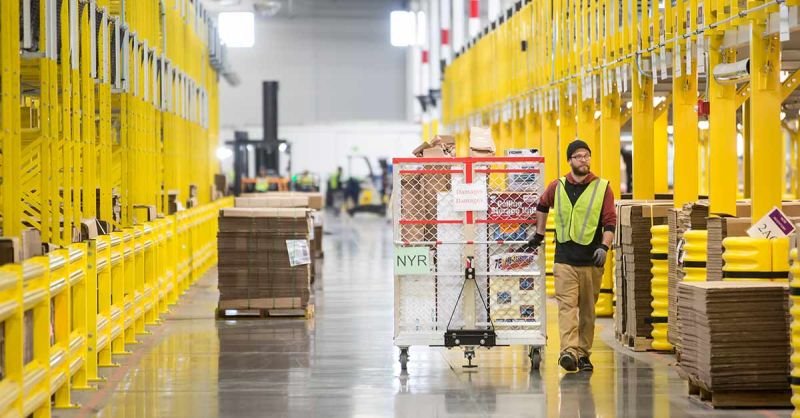
FAQ
What are the six factors of reverse logistics?
Six factors play a crucial role in effective reverse logistics management:
1. Return policies and procedures: Clear and well-defined return policies and procedures are essential for guiding customers on how to return products, setting expectations, and streamlining the returns process.
2. Communication and collaboration: Effective communication and collaboration between different departments and stakeholders help ensure smooth handling of returned products, minimize delays, and improve overall efficiency.
3. Technology integration: Leveraging technology solutions, such as barcode scanning and automated data management systems, can enhance visibility, accuracy, and speed in the reverse logistics process.
4. Customer satisfaction: Prioritizing customer satisfaction by simplifying the return process, promptly processing returns, and providing clear communication can lead to increased loyalty and positive brand reputation.
5. Performance measurement: Defining key performance indicators, regularly analyzing data, and implementing continuous improvement initiatives are essential for optimizing reverse logistics processes and driving efficiency.
6. Cost savings and value recovery: By focusing on recovering value from returned products, reducing waste, and minimizing losses, businesses can achieve cost savings and improve their bottom line through effective reverse logistics management.
What are the success factors in the concept of reverse logistics and its strategy?
Success factors in the concept of reverse logistics and its strategy lie in the seamless integration of key elements such as clear return policies, effective communication, technology utilization, customer satisfaction, performance measurement, and cost savings. These critical components form the foundation for a successful reverse logistics framework, where each aspect plays a vital role in optimizing the entire process.
Clear return policies serve as the guiding principles that set expectations for both customers and internal stakeholders, ensuring a smooth and consistent return process. Effective communication fosters collaboration between departments and partners, facilitating seamless coordination and problem-solving. Leveraging technology not only enhances visibility and accuracy but also enables real-time tracking and data management, leading to operational efficiency.
Customer satisfaction is paramount in reverse logistics, as a positive experience can result in increased loyalty and repeat business. By promptly processing returns, simplifying the return process, and providing clear communication, businesses can build trust and strengthen relationships with their customers.
Performance measurement through defined KPIs and data analysis allows for continuous improvement and informed decision-making. By identifying areas of inefficiency and implementing targeted improvements, businesses can enhance their processes and drive operational excellence. Finally, cost savings and value recovery are achieved through a focus on reducing waste, recovering value from returned products, and optimizing resource allocation.
By prioritizing these success factors and integrating them cohesively into their reverse logistics strategy, businesses can not only navigate the complexities of reverse logistics effectively but also achieve sustainable cost savings, improve customer satisfaction, and drive success in their supply chain operations.
What is critical success factors in logistics?
Critical success factors in logistics refer to the key elements that are essential for achieving success in managing the flow of goods and services throughout the supply chain. These factors include efficient transportation, accurate inventory management, effective communication, streamlined processes, and strong relationships with suppliers and partners. By focusing on these critical success factors, businesses can optimize their logistics operations, reduce costs, improve customer satisfaction, and ultimately drive success in their supply chain management. Embracing these factors and incorporating them into logistics strategies can help businesses stay competitive, adapt to changing market conditions, and achieve long-term success in the fast-paced world of supply chain management.
What are the 6 R’s of logistics?
The 6 R’s of logistics refer to the key principles that guide effective reverse logistics management: Return policies and procedures, Communication and collaboration, Technology integration, Customer satisfaction, Performance measurement, and Cost savings and value recovery. These factors work together to streamline processes, enhance customer experience, and drive efficiency in managing returned products. By prioritizing these principles, businesses can optimize their reverse logistics strategies, reduce costs, and ultimately improve their supply chain operations.
Hope this article was helpful for more checkout our previous blog post by clicking here