
Key Takeaways:
- Reverse Logistics is a critical component of supply chain management that involves transporting items from the customer back to the producer or merchant.
- Streamlining reverse supply chain procedures can help firms save money, increase customer happiness, and reduce environmental impact.
- The challenges of reverse logistics include processing returns, restoring or disposing of products, and organizing transportation.
- Automation, data analytics, and cooperation are examples of innovative ways to streamline reverse logistics operations.
- Technology integration is critical for enhancing reverse supply chain processes by enabling real-time tracking, increased visibility, and efficient communication.
- Implementing best practices such as developing a clear reverse logistics strategy, forming collaborations with third-party suppliers, and prioritizing customer experience can all contribute to successful reverse logistics management.
Businesses that embrace innovation and overcome hurdles can unlock the promise of reverse logistics and establish a more sustainable supply chain.
Introduction
Reverse logistics is an important part of the supply chain that manages the movement of products from the customer back to the producer or merchant. This procedure entails handling returned, damaged, or defective goods, as well as coordinating recycling or disposal. Reverse supply chain contributes significantly to customer happiness, cost reduction, and sustainability.
In this blog post, we will look at the importance of reverse logistics in the United States, the issues that come with it, and innovative ways for optimizing the process. We will also talk about how to integrate technology into reverse supply chain and highlight best practices for successful reverse logistics management. By the conclusion, you’ll have a thorough understanding of how to optimize reverse logistics operations and embrace innovation. the USA.
Understanding the Importance of Reverse Logistics
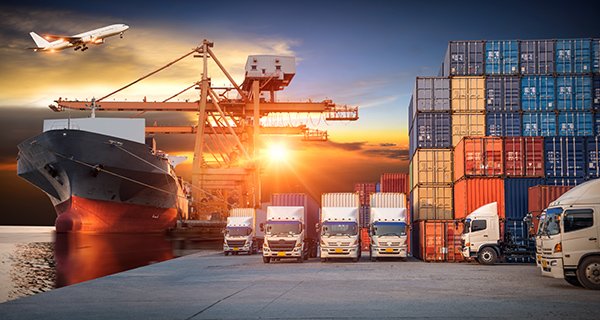
Reverse supply chain is necessary for a variety of reasons. For starters, it enables businesses to manage returned products more effectively, lowering the financial impact of returns while increasing customer satisfaction. Companies that process returns and replacements efficiently can sustain client loyalty and improve their reputation.
Second, reverse logistics helps to reduce costs while also increasing sustainability. Businesses can reduce waste and environmental impact by refurbishing, recycling, or disposing of their products properly. Companies can recoup value from returned products while also lowering inventory holding costs by managing reverse logistics.
Finally, reverse supply chain gives useful information about product quality, customer behavior, and supply chain inefficiencies. Return data analysis allows firms to uncover patterns and make informed decisions to improve product design, packing, and delivery operations.
Challenges Faced in Reverse Logistics
- Reverse logistics presents various problems that organizations must solve.
- Effective return management is one of the key challenges. Companies must create effective return processes, which include authorization, inspection, and disposal of returned products.
- Another problem is the refurbishment or disposal of returned products. This method necessitates a thorough assessment of the product’s state to determine whether it can be fixed, reconditioned, or disposed of properly.

- Another challenge is Managing the reverse supply chain. It can likewise be difficult, as it requires coordination with numerous partners and transportation providers.
- Reverse supply chain also necessitates excellent communication and collaboration among numerous stakeholders, including customers, manufacturers, retailers, and logistics providers. Successful operations require a smooth flow of information and fast resolution of concerns.
- Finally, reverse logistics necessitates accurate tracking and visibility of returns. Companies must have systems in place to track the status and location of returned items, allowing for more efficient processing and fewer delays.
Innovative Solutions for Streamlining Reverse Logistics
Innovation is essential for simplifying reverse logistics procedures.
Automation is a new approach that can considerably boost efficiency. Automated systems can handle duties like return authorization, product inspection, and sorting, which reduces manual work and human error.
Data analytics is another effective method for optimizing reverse supply chain operations. Businesses that analyze return data can obtain insights into the causes of returns, uncover patterns, and make data-driven decisions to improve product quality and customer happiness.

is also vital for improving reverse supply chain. Building good partnerships with third-party providers, suppliers, and customers can improve coordination and information sharing, resulting in faster issue resolution and increased efficiency.
Furthermore, using emerging technologies like Internet of Things (IoT) devices, blockchain, and artificial intelligence can transform the reverse supply chain. Real-time tracking, safe and transparent transactions, and predictive analytics can all help to improve the efficiency and reliability of reverse supply chain procedures.
Technology Integration in Reverse Logistics
Technology integration is critical to streamlining reverse supply chain procedures.

By leveraging technology, businesses may increase tracking, visibility, and communication throughout the reverse supply chain.
Real-time monitoring solutions enable businesses to monitor the status and location of returned products, allowing for more efficient processing and fewer delays. This visibility also allows for proactive engagement with clients, including updates on return status and expected resolutions.
Integration with customer relationship management (CRM) systems helps improve the reverse supply chain process. Companies can get insights into customer behavior, preferences, and trends by tying return data to customer profiles, allowing for more tailored customer experiences and targeted marketing campaigns.
Furthermore, technological integration facilitates data analytics, which can yield significant insights from return data. Companies can discover the fundamental causes of returns by evaluating patterns and trends, making informed decisions to improve product quality, and identifying process optimization opportunities.
And Lastly, digital integration promotes collaboration among stakeholders in the reverse supply chain.
Businesses that deploy cloud-based platforms or shared digital ecosystems can improve communication, share information in real time, and collaborate on issue resolution.
Best Practices for Successful Reverse Logistics Management
Businesses can achieve successful reverse supply chain management by following a few best practices:
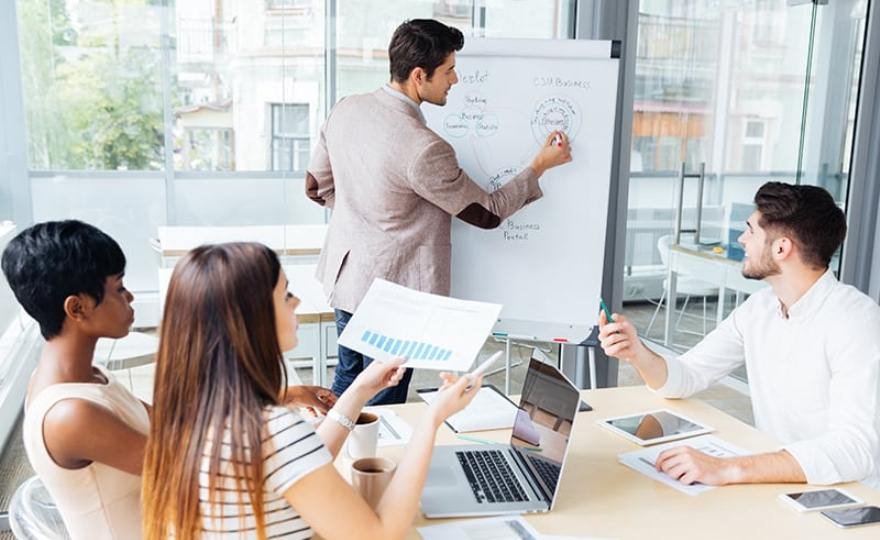
1. Create a clear reverse logistics strategy. Define goals, methods, and key performance indicators (KPIs) to help manage and optimize reverse logistics operations.
2. Form partnerships with third-party providers. Collaborate with logistics providers, refurbishment firms, and recycling facilities to benefit from their experience and resources in managing returned products.
3. Prioritize the client experience: Create return processes that are easy, convenient, and user-friendly. To improve customer satisfaction, provide clear return instructions, effective contact channels, and timely resolutions.
4. Use data analytics: analyze return data to uncover trends, root causes, and areas for improvement. Use data insights to improve product quality, packaging, transportation, and reverse logistics processes.
5. Implement effective product disposition strategies. Thoroughly assess returned products to determine the appropriate course of action, whether refurbishing, resale, recycling, or disposal. Maximize value recovery while minimizing waste.
6. Continuously monitor and improve: Evaluate reverse logistics performance on a regular basis, measure key performance indicators, and put continuous improvement plans into action. Embrace feedback from consumers and stakeholders to promote innovation and enhance operations.
Businesses that implement these best practices can successfully manage reverse supply chain processes, lower costs, boost customer happiness, and drive sustainability.
Conclusion
Streamlining reverse supply chain operations is critical for firms in the United States to overcome obstacles and embrace innovation. Companies may optimize their operations, save costs, increase customer happiness, and contribute to a more sustainable supply chain by understanding the relevance of reverse logistics, identifying and addressing the difficulties that arise, and adopting new solutions.
Businesses may realize the full potential of reverse logistics by integrating technology, real-time tracking, data analytics, and collaboration. This will provide significant insights into product quality, customer behavior, and supply chain efficiency. Companies may maintain a competitive advantage in the dynamic field of reverse logistics by establishing best practices and constantly upgrading.
To summarize, by overcoming hurdles and embracing innovation, firms may streamline reverse supply chain in the United States and create a more efficient, customer-centric, and sustainable supply chain.
FAQ
What are the key challenges to implementing a reverse logistics system?
Effective return management is a major difficulty when building a reverse supply chain system.
- Creating effective return processes, such as permission, inspection, and disposition of returned products, can be difficult and time-consuming.
- Another problem is refurbishing or disposing of returned items, which requires a comprehensive review of the product’s condition and selecting the best course of action.
- Coordinating with various partners and transportation providers in the reverse supply chain can also be difficult, as effective communication and teamwork are required for successful operations.
- Finally, proper monitoring and visibility of returned products is critical for efficient processing and reducing delays; therefore, organizations must have systems in place to monitor the status and location of returned items.
Overcoming these obstacles is critical for firms looking to optimize reverse logistics processes and drive sustainability in their supply chains.
What is reverse logistics, and how can reverse logistics activities help achieve sustainability?
Reverse logistics is an important aspect of supply chain management that focuses on processing returns, refurbishing or disposing of products, and optimizing the flow of goods in the reverse supply chain.
Businesses may improve their reverse supply chain operations by examining return data and using new solutions such as automation, data analytics, and technology integration. These initiatives not only improve operating efficiency, but they also significantly contribute to meeting sustainability objectives. Companies may save money, decrease waste, improve customer happiness, and contribute to a more sustainable supply chain by prioritizing the customer experience, optimizing product disposition plans, and continuously monitoring and improving procedures.
Businesses in the United States can promote innovation, increase sustainability, and gain a competitive advantage in a dynamic environment by using effective reverse logistics management.
What are the factors for successful reverse logistics implementation?
Several factors influence the successful adoption of reverse logistics.
- Creating a clear strategy with defined goals, processes, and key performance indicators is critical for directing and managing reverse logistics operations.
- Partnering with third-party suppliers, refurbishment businesses, and recycling facilities can help you take advantage of their experience and resources when dealing with returned products.
- Prioritizing the customer experience by creating simple return processes, clear instructions, effective communication channels, and quick remedies will boost customer satisfaction.
- The use of data analytics to examine return data, discover trends, root causes, and improvement possibilities is critical for optimizing product quality, packing, shipping, and reverse logistics.
- Implementing effective product disposition strategies, such as refurbishment, resale, recycling, or disposal, can maximize value recovery while reducing waste.
- Continuously monitoring and improving reverse logistics performance, measuring KPIs, and implementing continuous improvement projects are critical for generating innovation, improving operations, and succeeding in reverse logistics management.
What are the barriers to effective reverse logistics?
Despite the various advantages of using technology in reverse supply chain processes, there are a number of obstacles that can impede efficient operations.
- One key difficulty is a lack of real-time tracking systems and visibility throughout the reverse supply chain, which can cause delays and inefficiencies when processing returned products.
- Furthermore, the complexity of managing returns, repairing things, and working with various partners in the reverse supply chain network can create substantial challenges.
- Another impediment is the difficulty of assessing and utilizing data from return procedures to drive changes and optimize operations.
Businesses may struggle to overcome these constraints and fully realize the promise of reverse supply chain unless they have a clear plan, efficient product disposition processes, and ongoing monitoring and improvement projects.