Key takeaways
Reverse logistics processes must handle repair difficulties well if they are to continue operating efficiently and satisfying customers in the fast-paced business climate of today. This procedure involves a lot of warranty and repair management, which makes sure that the products are handled carefully and methodically. Businesses that comprehend the value of warranty and repair management are able to maximize profits, reduce expenses, and retain customer loyalty. Reducing the frequency and severity of repairs can be achieved by putting proactive measures into place, such as making investments in quality control and product design, supplying extensive product documentation, and providing regular maintenance services. Utilizing technology to improve customer satisfaction and expedite maintenance procedures is possible. Examples of this technology include automated tracking systems and diagnostic tools. Working together with service providers, keeping an eye on things constantly, and improving repair performance are also key strategies for efficient repair operations in reverse logistics. By focusing on these key takeaways, companies can optimize their repair processes, reduce costs, and ensure customer satisfaction in the reverse logistics journey.
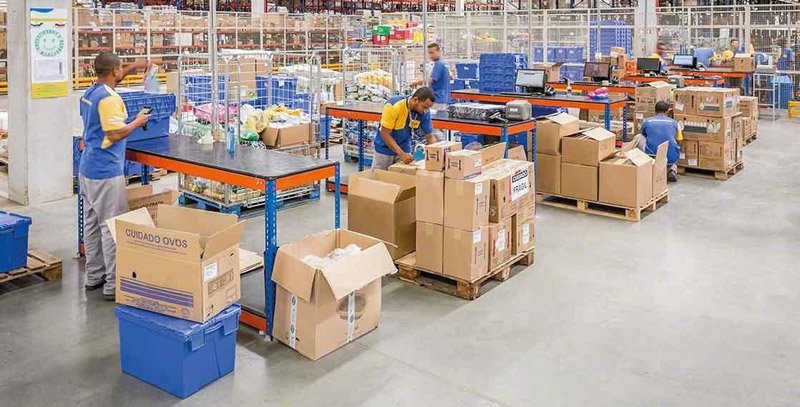
Introduction
The administration of warranties and repairs is essential to preserving customer satisfaction and operational effectiveness in the fast-paced field of reverse logistics. Establishing an organized procedure is essential for managing issues arising from returned goods or repairs. Companies that understand the importance of warranty and repair management can increase revenue and minimize expenses while also fostering customer loyalty through satisfactory repair experiences. The optimization of repair operations and the assurance of a smooth voyage through reverse logistics necessitate the implementation of proactive measures, technology utilization, collaboration with service partners, and ongoing monitoring and improvement of repair performance. Businesses can improve customer satisfaction, cut expenses, and streamline processes by concentrating on five important factors.
Understanding the importance of warranty and repair management in reverse logistics
The administration of warranties and repairs is essential to reverse logistics in order to maintain both operational effectiveness and customer happiness. To properly tackle these problems, a methodical approach must be in place for returning or repairing products.
The maintenance of client loyalty is a primary benefit of warranty and repair management in reverse logistics. Customers are more inclined to trust the business and make additional purchases in the future when they have a pleasant experience with the repair procedure. However, a bad repair experience might make a consumer angry and give them a bad impression of the business.
Furthermore, warranty and repair management has the potential to reduce expenses and increase profitability in reverse logistics. Businesses can lower the quantity of inventory that needs to be written off as losses by managing repairs well. In addition, it minimizes the financial impact on the business by enabling improved tracking of warranty claims and guaranteeing that repairs are completed within the warranty period.
Overall, preserving customer pleasure, cutting expenses, and enhancing operational effectiveness all depend on a knowledge of the significance of warranty and repair management in reverse logistics.
Implementing proactive measures to reduce repair challenges
The implementation of proactive procedures aimed at reducing the frequency and severity of repairs is crucial for the proper handling of repair difficulties in reverse logistics. Businesses can increase overall efficiency and lessen the impact of repairs on their operations by being proactive.
Investing in quality control and product design is one proactive step. Businesses may reduce the possibility that repairs will be required in the first place by developing their goods with durability and reliability in mind. During the product development phase, this can be accomplished by strict testing and quality assurance procedures.
Including thorough user manuals and product documentation is another preventative step. Customers can minimize the danger of damage or overuse that may necessitate repairs by following clear and comprehensive instructions, which can aid in proper product usage. Further lowering the need for repairs is the ability to help consumers solve small problems on their own by offering troubleshooting guidance.
Reducing repair issues can also be achieved by preventive servicing and routine maintenance. Companies are able to detect any problems before they become serious ones and offer preventative servicing solutions and periodic maintenance programs. This strategy prolongs the life of the items while also assisting in minimizing downtime for clients.
Businesses can dramatically lower maintenance issues in reverse logistics by putting these preventative measures in place, which will increase operational efficiency. and customer satisfaction.
Leveraging technology for streamlined repair processes
Utilizing technology to streamline reverse logistics repair operations is crucial in the current digital environment. Employing cutting-edge equipment and software can help businesses increase the efficacy and efficiency of their repair processes.
Automated tracking and documentation systems are one method that technology can simplify the repair process. Employing a computerized system to manage the state of repairs allows businesses to keep an easy eye on things, spot bottlenecks, and guarantee on-time completion. This enhances openness and makes it possible to communicate with clients about the progress of repairs more effectively.
The usage of diagnostic tools and remote troubleshooting capabilities is another technology-driven strategy. Businesses may remotely diagnose problems, give clients real-time advice, and, in certain cases, start remote repairs with the aid of diagnostic software and linked devices. This improves the customer experience with repairs overall while also saving time and money.
Technology can also make component monitoring and inventory management more effective. Businesses can make sure they have the replacement parts needed for repairs on hand by putting in place an integrated system that monitors inventory levels. This lowers the lead time for repairs and raises client contentment.
Businesses can achieve quicker turnaround times, increased accuracy, and a better customer experience in reverse logistics by utilizing technology to expedite repair procedures.
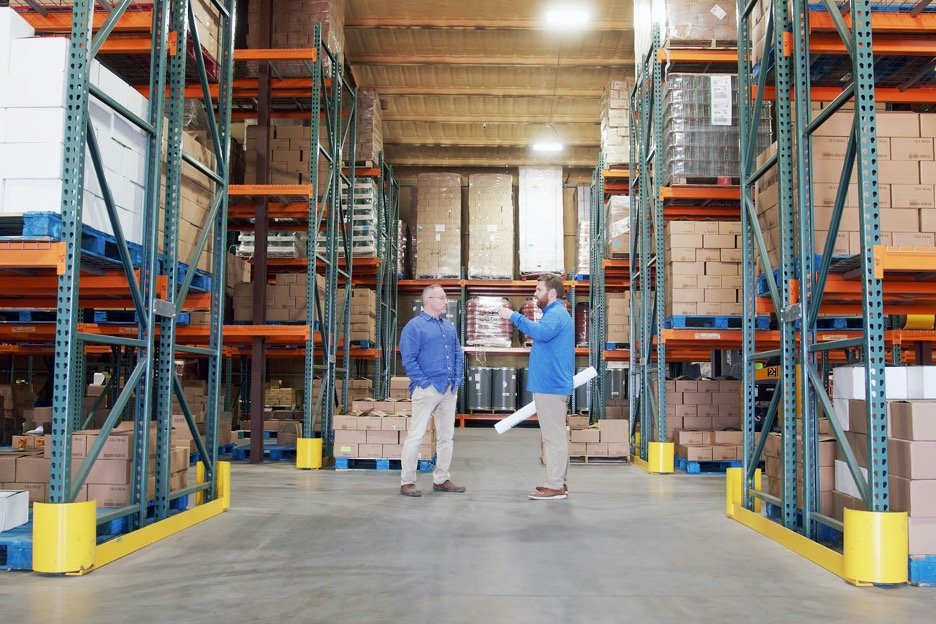
Collaborating with service partners for efficient repairs
In reverse logistics, working together with service partners is a smart way to guarantee effective repairs. Companies can improve the repair process by leveraging their resources and experience by forming partnerships with reputable and experienced service providers.
Working with service partners gives you access to specific expertise and abilities. Because they frequently have a great deal of experience fixing particular brands or product categories, service partners can identify and fix problems fast. This knowledge can greatly shorten repair turnaround times while raising the standard of repairs as a whole.
Service partners can also provide flexibility and scalability for repair operations. Service partners can swiftly scale up to manage an increase in workload when businesses encounter a spike in repair requests. This guarantees that repairs are finished in the anticipated timeframes and prevents any backlog of pending repairs.
Companies can access their network of suppliers for spare parts by working with service partners. Because they frequently have long-standing connections with suppliers, service partners can quickly and effectively find authentic, high-quality spare parts. This lowers the possibility of additional damage or reoccurring problems by ensuring that repairs are made with the appropriate parts.
Companies can streamline their repair procedures, cut expenses, and offer their clients effective repair services by working with service partners.
Continuous improvement and monitoring of repair performance
In reverse logistics, it is crucial to continuously assess repair performance and find areas for improvement in order to guarantee consistent client satisfaction.
Regularly assessing repair processes’ performance is one way to achieve continual improvement. Businesses can determine areas that require improvement by examining important data like repair turnaround time, customer satisfaction scores, and repeat repair rates. Finding bottlenecks, inefficiencies, or training gaps that might be affecting repair performance is possible with the aid of this investigation.
Companies might launch focused improvement projects based on the results of performance reviews. This could entail investing in new tools or equipment to increase efficiency, streamlining repair workflows, or giving repair staff more training. To be sure that these efforts are having the desired effect, it is imperative that their effects be regularly monitored. the desired results.
Another important factor in the ongoing enhancement of repair performance is customer feedback. Through proactive feedback collection from customers who have experienced the repair process, businesses can pinpoint particular issues or potential areas for enhancement. Direct contact routes, internet reviews, and questionnaires can all be used to get this input. Building trust is facilitated by responding to consumer input and making the required adjustments. This shows a dedication to meeting customer needs.
Businesses should make sure that their reverse logistics operations continue to be effective, customer-focused, and compliant with industry best practices by regularly assessing and enhancing repair performance.
Conclusion
In summary, it is clear that warranty and repair management play a critical role in reverse logistics and that their significance cannot be understated. Businesses can improve customer satisfaction, cut expenses, and streamline processes by concentrating on five important factors. The key to attaining operational efficiency and customer happiness is to collaborate with service partners, assess and improve repair performance regularly, implement proactive measures, and utilize technology. Businesses will surely succeed or fail based on their ability to comprehend the importance of warranty and repair management as they attempt to manage the intricacies of reverse logistics.
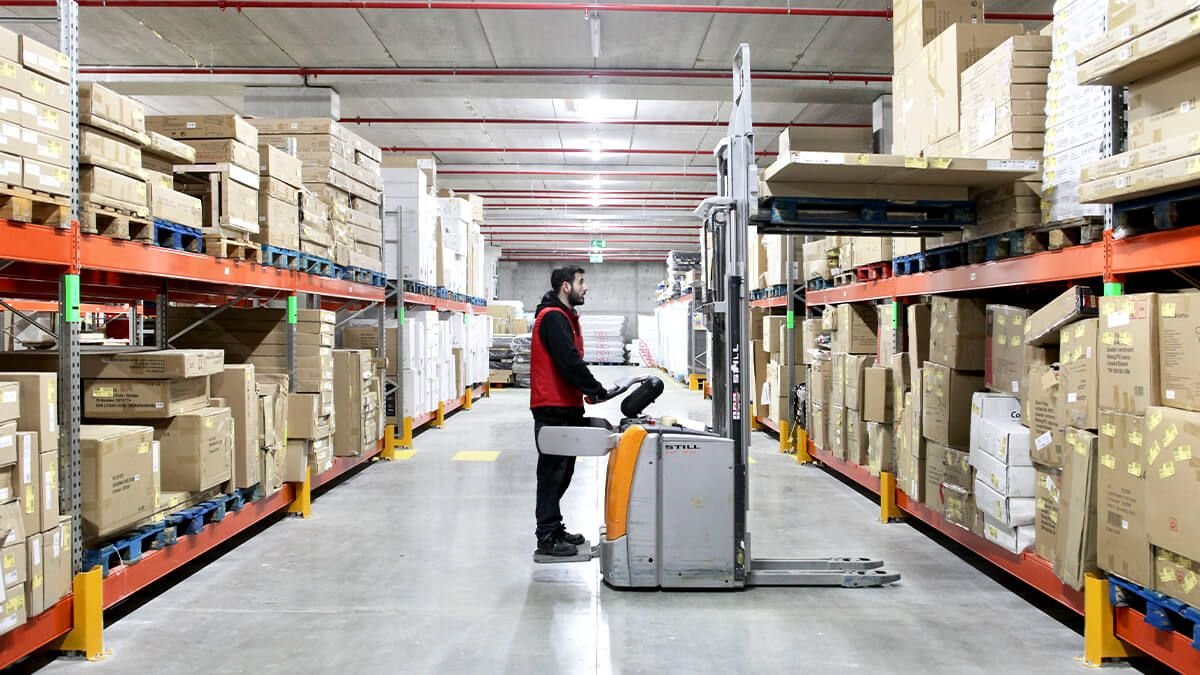
FAQ
What are the primary challenges when it comes to reverse logistics?
The main obstacles in reverse logistics are processing returns in an elaborate manner, handling defective products in an intricate manner, and effectively organizing repairs. Reverse logistics entails managing a range of stakeholders, including suppliers, customers, and service partners, in order to guarantee a smooth and uninterrupted return of goods into the supply chain. Furthermore, effective tracking and management of warranty claims, repairs, and spare parts inventory necessitate meticulous attention to detail in reverse logistics. In order to preserve operational effectiveness, cut expenses, and deliver a satisfying customer experience in the reverse logistics process, businesses must overcome these obstacles.
Is one motivation for reverse logistics is warranty repair or replacement?
Reverse logistics is in fact one reason to engage in warranty repair or replacement. When warranty-covered faults occur on items, businesses need to handle returns, repairs, and replacements in an efficient manner. Companies may preserve their dedication to customer pleasure, protect their brand’s reputation, and adhere to regulatory requirements by handling warranty claims in an efficient manner. In order to ensure that consumers obtain prompt and satisfactory fixes to product concerns and eventually contribute to a positive overall customer experience, warranty repair and replacement play a vital part in reverse logistics.
Which of the following is a difficulty in reverse logistics?
Overseeing the complex process of handling faulty products and arranging repairs is one challenge in reverse logistics. Ensuring a smooth flow of products back into the supply chain requires managing the intricacies of warranty claims, spare parts inventory, and repair processes. Companies must handle warranty replacements and repairs effectively if they want to fulfill their legal requirements, preserve their brand’s reputation, and satisfy customers. In order to save expenses, preserve operational effectiveness, and give customers a great experience throughout the repair process, reverse logistics must overcome these obstacles.
What are the 5 R’s of reverse logistics?
The fundamental ideas that direct the handling of product returns and repairs in the supply chain are referred to as the “5 R’s” of reverse logistics. Among these guidelines are:
1. Returns: This is the procedure for managing consumer product returns, making sure that things are successfully and efficiently reintegrated into the supply chain.
2. Repairs: One of the most important aspects of reverse logistics is fixing damaged or defective products. Ensuring that products are restored to functioning condition and efficiently organizing repairs are critical to preserving client happiness.
3. Refurbishment: Refurbishing products is bringing them back to their original state, frequently by replacing, cleaning, or repairing parts. This contributes to extending product lifecycles and cutting down on supply chain waste.
4. Recycling: Recycling is the conscientious discarding of goods that are beyond repair or refurbishment. This procedure lessens the influence on the environment by ensuring that materials are recycled or disposed of in an ecologically responsible way.
5. Redistribution: Goods can be reintroduced into the supply chain for reuse or resale once they have been mended, refurbished, or recycled. By taking this action, waste is reduced and the value of returned goods is increased.
Businesses may efficiently handle product returns, repairs, and refurbishments while simultaneously fostering sustainability and cutting waste in the supply chain by adhering to the five rules of reverse logistics. Enhancing efficiency, cutting costs, and increasing customer satisfaction are all possible outcomes of implementing these concepts into reverse logistics operations.
Hope this article was helpful for more check out our previous blog post by clicking here