Key takeaways :
- Key takeaways are concise summaries of important points or insights from a presentation, meeting, article, or event.
- They help distill complex information into easily understandable and actionable points.
- Key takeaways are often presented in threes, following the “Rule of 3” for effective communication.
- They provide a record of decisions, rationale, and action items discussed during meetings.
- Key takeaways can be a single idea or point that is the most important or impactful.
- They contribute to progress, success, and growth by focusing on the essential information.
- Key takeaways can be used to guide decision-making, improve understanding, and drive success.
- They are valuable for referencing, revisiting, and sharing important insights with stakeholders.
- Key takeaways can be applied to various contexts, including business, sports, education, and personal development.

In today’s dynamic business environment, an effective reverse logistics system is crucial for companies to efficiently manage product returns and optimize their supply chain. In this blog post, we will explore the essential elements that make up a successful reverse logistics system, enabling businesses to streamline their operations and enhance customer satisfaction.
Objective 1: Seamless Returns Process
An essential element of an effective reverse logistics system is a seamless returns process. This involves providing customers with clear instructions and user-friendly platforms for initiating returns. By simplifying the returns process, businesses can reduce customer frustration, improve turnaround times, and enhance overall customer satisfaction.
Objective 2: Efficient Product Sorting and Inspection
Another crucial element is the efficient sorting and inspection of returned products. Implementing standardized procedures and utilizing advanced technologies such as barcode scanning and automated sorting systems can significantly improve accuracy and speed in the evaluation and categorization of returned items. This ensures that products are appropriately handled, whether they require repairs, refurbishment, recycling, or disposal.
Objective 3: Robust Inventory Management
Effective reverse logistics relies on robust inventory management. It is essential to have a real-time inventory tracking system that allows businesses to monitor and control the flow of returned products accurately. By maintaining accurate inventory records, companies can optimize space utilization, minimize stockouts, and ensure timely replenishment of refurbished or resold items.
Objective 4: Collaborative Partnerships
Collaboration with strategic partners is a vital element of an effective reverse logistics system. Engaging with logistics service providers, refurbishers, recyclers, and other stakeholders can streamline the reverse flow of goods and expedite the entire process. By establishing strong partnerships, businesses can leverage the expertise and resources of these external entities to enhance efficiency and reduce costs.
Objective 5: Data Analytics and Continuous Improvement
Data analytics plays a pivotal role in optimizing reverse logistics. By analyzing data on returns, product quality, customer feedback, and other relevant metrics, businesses can identify patterns, trends, and areas for improvement. This data-driven approach enables companies to make informed decisions, implement process enhancements, and continually refine their reverse logistics system for better performance and customer satisfaction.
Building an effective reverse logistics system is a critical component of successful supply chain management. By incorporating essential elements such as a seamless returns process, efficient product sorting and inspection, robust inventory management, collaborative partnerships, and data analytics, businesses can streamline their operations, reduce costs, and enhance customer satisfaction.
Remember, a well-designed reverse logistics system not only helps businesses handle product returns effectively but also provides valuable insights for process improvements, sustainability initiatives, and overall supply chain optimization.
To learn more about implementing an effective reverse logistics system or to get expert guidance tailored to your business needs, reach out to [Your Company Name], a trusted leader in supply chain solutions.
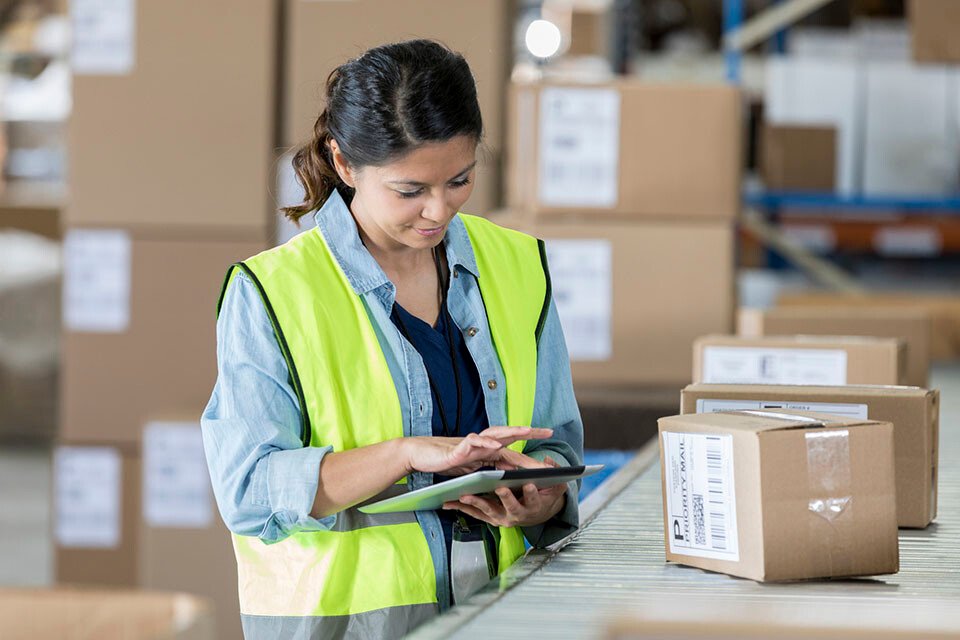
FAQ
What are the elements of reverse logistics management?
Reverse logistics management encompasses several key elements. These elements include a seamless returns process, efficient product sorting and inspection, robust inventory management, collaborative partnerships, data analytics, and continuous improvement. These components are essential for businesses to effectively handle product returns, optimize inventory, reduce costs, and enhance customer satisfaction. Implementing these elements can help streamline operations, improve sustainability practices, and drive overall supply chain optimization.
What are the five 5 elements of logistics?
The five elements of logistics are as follows:
- Planning: This element involves activities such as storage, warehousing, and materials handling. It focuses on creating consistency in the movement of goods and understanding how logistics activities contribute to the overall supply chain.
- Inventory: Inventory management is closely related to storage and warehousing. It involves determining what stock to hold, where it should be located, and how much stock to hold. Effective inventory management ensures the proper control of goods flowing in and out of warehouses.
- Transportation: Transportation is a crucial element of logistics and encompasses all modes of transport, including road vehicles, freight trains, cargo shipping, and air transport. It ensures that goods are delivered to the right location, at the right time, and in the ideal condition.
- Packaging: Packaging logistics is responsible for ensuring that products are properly packaged to maintain their quality throughout the supply chain. It involves selecting appropriate packaging materials and methods to protect goods during transportation and storage.
- Information Handling: Information handling is an essential element that involves managing data related to logistics activities. It includes tracking shipments, monitoring inventory levels, analyzing customer demand, and utilizing technology to improve visibility and decision-making.
These five elements work together to ensure the smooth flow of goods, optimize inventory levels, minimize costs, and meet customer demands within the logistics process.
What are the 5 R’s of reverse logistics?
The five R’s of reverse logistics are as follows:
- Returns: The first step in the reverse logistics process is handling product returns. This involves establishing efficient processes for receiving, inspecting, and testing returned products.
- Reselling: Reselling refers to the process of refurbishing or reconditioning returned products that are still in good condition and suitable for resale. This helps businesses recoup value from returned items and reduce losses.
- Repairs: Repairing involves fixing any defects or damages in returned products that can be repaired. This allows businesses to salvage and restore the functionality of the items, reducing waste and maximizing asset recovery.
- Replacements: Replacements involve providing customers with new or equivalent products in exchange for their returned items. This ensures customer satisfaction and helps maintain loyalty.
- Recycling: Recycling is the final step in the reverse logistics process. It involves properly disposing of returned products that cannot be resold, repaired, or reused. Recycling helps promote sustainability and reduces environmental impact.
These five R’s of reverse logistics provide a framework for businesses to effectively manage product returns, optimize value recovery, and minimize waste in the supply chain.
What are the 7 R’s of reverse logistics?
Implementing the 7 R’s of reverse logistics can come with its own set of challenges. While the specific challenges may vary depending on the industry and organization, here are some common challenges that businesses may face:
- Resource Allocation: Allocating sufficient resources, including time, budget, and personnel, to effectively plan and implement reverse logistics strategies can be challenging. Limited resources may hinder the ability to handle returns efficiently and optimize value recovery.
- Process Complexity: Reverse logistics involves multiple activities, such as returns management, repairs, repackaging, and recycling. Managing these processes and ensuring smooth coordination between different stages can be complex and require careful planning.
- Data Management: Effective reverse logistics relies on accurate and timely data management. Gathering and analyzing data related to returns, repairs, and inventory can be challenging, especially if the organization lacks robust data systems and analytics capabilities.
- Collaboration and Partnerships: Reverse logistics often involves collaboration with various stakeholders, including customers, suppliers, service providers, and recycling facilities. Establishing and maintaining effective partnerships can be challenging, particularly when different parties have different goals and processes.
- Customer Expectations: Meeting customer expectations in terms of returns processing, refunds, replacements, and overall customer service can be challenging. Providing a seamless and satisfactory experience for customers during the reverse logistics process is crucial for maintaining customer loyalty.
- Regulatory Compliance: Reverse logistics operations need to comply with various regulations related to product returns, recycling, and disposal. Staying up to date with changing regulations and ensuring compliance can be challenging, especially for organizations operating in multiple jurisdictions.
- Environmental Sustainability: Reverse logistics plays a significant role in promoting environmental sustainability by reducing waste and promoting recycling. However, implementing sustainable practices and managing the environmental impact of reverse logistics operations can be challenging, requiring careful planning and investment.
It is important for businesses to anticipate and address these challenges to ensure the successful implementation of the 7 R’s of reverse logistics. By developing robust processes, leveraging technology, fostering collaboration, and staying informed about industry best practices, organizations can overcome these challenges and optimize their reverse logistics operations.
Hope this article was helpful for more check out our previous blog post by clicking here.