Key takeaways
- One often-overlooked yet vital but challenging part of supply chain management is reverse logistics.
- The obstacles might be overwhelming, ranging from managing recycling and refurbishments to handling returns and repairs.
- On the other hand, businesses may streamline their reverse logistics procedures by utilizing data analytics, adopting technological solutions, and simplifying communication.
- Businesses may improve customer satisfaction, save waste, and boost efficiency in their reverse logistics operations by placing a high priority on open lines of communication, encouraging stakeholder participation, and consistently refining procedures.
- It’s time to bring reverse logistics to the forefront and realize its promise for a more seamless and sustainable supply chain.
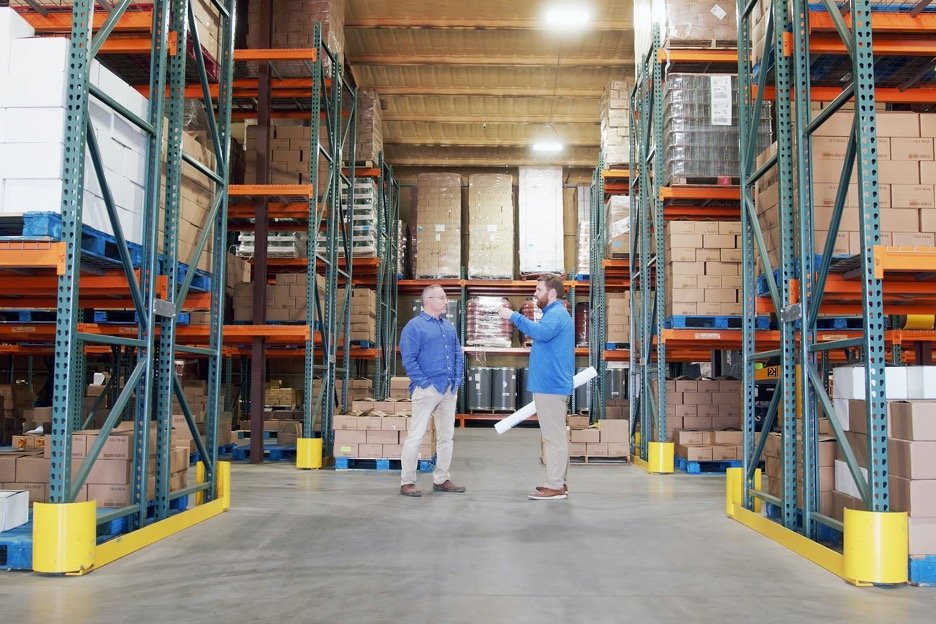
Introduction
One important but sometimes disregarded component of supply chain management is reverse logistics. It is clear that more effective procedures and more stakeholder communication are required when we examine the intricacies and difficulties of handling returns, repairs, and recycling. Businesses may improve customer satisfaction and manage their reverse logistics operations by utilizing data analytics, optimizing communication, and putting technological solutions into practice. It’s time to raise awareness of reverse logistics’ significance and realize its potential for a supply chain that is more smooth and sustainable.
Understanding the challenges in reverse logistics
The process of controlling the movement of goods from the point of consumption back to the point of origin is known as reverse logistics. It includes recycling, refurbishments, returns, and repairs. Reverse logistics offers a number of difficulties and bottlenecks even though it is essential to guaranteeing customer happiness and cutting waste.
Reverse logistics presents a number of difficulties, one of which is handling the complexity of managing several routes and parties. Coordination with clients, vendors, carriers, and service providers is necessary for the process because each has different needs and expectations. This intricacy may cause misunderstandings, inefficiencies, and delays.
The absence of traceability and visibility in reverse logistics presents another difficulty. In contrast to forward logistics, which follows a straight path from the producer to the final customer, reverse logistics entails a number of stops along the way. There are delays and uncertainty as a result of this lack of visibility in tracking and monitoring the status of returned goods.
Reverse logistics also frequently entails managing goods that are faulty, broken, or obsolete. Specialized knowledge and tools are needed for safe handling, testing, and disposal of this. Inadequate infrastructure and training may cause extra expenses and delays in the reverse logistics process.
Implementing technology solutions for efficiency
By using technological solutions, reverse logistics bottlenecks and inefficiencies may be addressed. Better coordination and decision-making are made possible by the real-time visibility and traceability of returned goods that advanced IT solutions may offer. Businesses can swiftly detect and eliminate bottlenecks because to these systems’ ability to track the location and condition of every item.
Utilizing robots and automation in reverse logistics processes is another technological approach. Returned product handling may be streamlined with the use of robotic arms and automated sorting systems, which will save labor costs and increase productivity. Additionally, these technologies may make inspections, repairs, and refurbishments quicker and more precise.
Additionally, putting in place a cloud-based platform or centralized database can help stakeholders collaborate and communicate more effectively. This facilitates the easy exchange of data, including product specifications, repair instructions, and customer feedback. By digitizing and standardizing these processes, companies can eliminate paperwork, reduce errors, and improve overall efficiency.
Streamlining communication and collaboration
It is imperative that businesses place a high value on efficient communication and teamwork in order to maximize reverse logistics operations. Establishing unambiguous lines of communication with suppliers, consumers, and service providers enables enterprises to guarantee a smooth exchange of information and prompt issue resolution. In addition to building trust, open communication improves the client experience in general.
In order to handle return requests and provide consumers with information on the status of returned goods, regular contact is essential. Businesses may establish connection and loyalty with their clients by providing them with updates at every stage. Additionally, arranging for repairs, replacements, or the disposal of returned goods requires prompt contact with suppliers and service providers. This proactive strategy reduces delays and streamlines the reverse logistics process.
Moreover, utilizing platforms and technologies for cooperation may help stakeholders share information and solve problems. Effective problem solving and prompt decision-making are made possible by real-time cooperation. Businesses may improve overall efficiency in reverse logistics operations, cut down on response times, and streamline their communication procedures by employing these solutions.
To sum up, efficient communication and teamwork are essential for maximizing reverse logistics operations. By emphasizing open lines of communication and encouraging cooperation amongst stakeholders, businesses may overcome obstacles and improve the efficiency of their reverse logistics operations.
In order to handle return requests and provide consumers with information on the status of returned goods, regular contact is essential. This can improve client satisfaction and foster a culture of trust. Coordinating repairs, replacements, or the disposal of returned goods requires prompt coordination with suppliers and service providers.
Furthermore, businesses may use platforms and tools for cooperation to help with information exchange and problem-solving. With the help of these technologies, stakeholders may collaborate in real time to solve problems and enhance procedures. Reverse logistics firms may improve overall productivity, eliminate mistakes, and shorten response times by optimizing communication and collaboration.
Leveraging data analytics for insights
Businesses may find opportunities for development and obtain important insights into their reverse logistics operations by utilizing data analytics. Businesses might identify patterns and trends that indicate frequent causes of returns or reoccurring problems with certain items by examining previous data on returns. With this data, data-driven choices and focused initiatives to lower returns and improve product quality may be put into practice.
For example, businesses may take proactive steps like investing in better size charts or offering clearer product descriptions to alleviate customer misunderstanding if data analysis reveals that a certain product category has a high return rate because of sizing concerns. Businesses may keep ahead of trends and make wise decisions to improve their reverse logistics by consistently collecting and evaluating data. processes.
Furthermore, inventory management in reverse logistics may be optimized by the application of data analytics. Businesses may identify the best inventory levels and resource allocation by examining demand trends and return cycle durations. This can save storage expenses, cut down on stockouts, and increase the effectiveness of inventories as a whole. Businesses may promote continuous development and increase the efficiency of their reverse logistics operations by utilizing data analytics.
These insights may be applied to specific tactics for lowering returns and raising the caliber of products, as well as to data-driven decision-making. To cut down on consumer uncertainty, the business should, for instance, invest in better size charts or give clearer product descriptions if a particular product category has a high return rate because of sizing concerns.
Additionally, inventory management in reverse logistics may be optimized through the use of data analytics. Businesses may identify the best inventory levels and resource allocation by examining demand trends and return cycle durations. This can save storage expenses, cut down on stockouts, and increase the effectiveness of inventories as a whole.
Continuous improvement strategies for better performance
To increase performance in reverse logistics, there must be constant improvement. Businesses should routinely assess their procedures, pinpoint opportunities for development, and put remedial measures in place.
Regularly auditing and reviewing the reverse logistics process’s performance is one method for continual improvement. This can assist in locating inefficiencies, bottlenecks, and non-compliant places. Companies might adopt process changes, offer more training, or modify performance measures in light of the findings.
Establishing an innovative and ongoing learning culture within the company is another tactic. Employee collaboration, experimentation, and learning from mistakes may result in innovative processes and creative solutions. It is important to aggressively seek out and include employee comments and recommendations in the process of improvement.
Businesses can also compare their performance in reverse logistics to rivals’ and the industry’s best practices. This can assist in identifying opportunities for improvement and gaps within the organization. Businesses should continually aim for improved performance in reverse logistics by establishing performance goals and tracking their success.
Conclusion
To summaries, the optimization of reverse logistics operations necessitates a diverse strategy comprising the implementation of technological solutions, optimization of communication and cooperation, utilization of data analytics for insights, and ongoing process improvement. Through emphasizing unambiguous communication channels, encouraging stakeholder engagement, and using data-driven insights, businesses may surmount obstacles, minimize returns, augment product quality, and optimize overall efficiency in reverse logistics. In order to perform better in reverse logistics, businesses must continuously assess their operations, encourage innovation, and compare their results to industry best practices. Businesses may improve customer satisfaction, cut expenses, and streamline processes by approaching reverse logistics holistically.
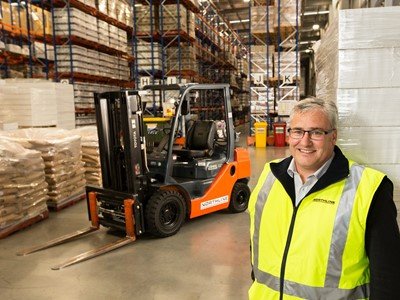
FAQ
How do you solve reverse logistics problems?
Technology solutions are one useful tool for resolving issues with reverse logistics. In order to overcome bottlenecks and inefficiencies, firms may better coordinate and make informed decisions by adopting modern software solutions for real-time visibility and traceability of returned items. Robotics and automation can help expedite the handling of returned goods, lowering labor costs and increasing productivity. Furthermore, improved communication and cooperation among stakeholders can be facilitated by a centralized database or cloud-based platform, enabling smooth information exchange and established procedures.
Simplifying cooperation and communication is also essential for resolving issues with reverse logistics. Having open lines of contact with clients, vendors, and service providers guarantees information flow and prompt problem solving. While prompt contact with suppliers and service providers helps plan repairs, replacements, or disposal of returned items, regular communication with consumers regarding return requests and product updates fosters confidence and loyalty.
Last but not least, using data analytics may offer insightful information about reverse logistics operations, assisting businesses in identifying areas for development and making data-driven choices. Businesses may use focused tactics for lowering returns and improving product quality by examining past return data to identify patterns and trends. A culture of innovation, frequent performance evaluations, benchmarking against industry best practices, and other methods of continuous improvement can all contribute to improved performance in reverse logistics operations. Employing a comprehensive strategy that integrates data analytics, communication tactics, technological solutions, and ongoing development allows businesses to maximize productivity and overcome reverse logistics issues.
How can reverse logistics be improved?
To increase productivity and cut expenses, businesses may optimize their reverse logistics procedures in a number of ways. Prioritizing open lines of communication and encouraging stakeholder cooperation are two important tactics. Employing technological solutions, such platforms and tools for collaboration, allows businesses to share information more easily, expedite decision-making, and improve communication procedures. In the process of reverse logistics, real-time cooperation may assist overcome obstacles and facilitate effective issue resolution.
In addition to communication and collaboration, leveraging data analytics is crucial for gaining valuable insights into reverse logistics operations. By analyzing historical data on returns, companies can identify patterns and trends that reveal common reasons for returns or recurring issues with specific products. This information can be used to make data-driven decisions and implement targeted strategies to reduce returns and enhance product quality.
Continuous improvement is also key in improving reverse logistics operations. By conducting regular performance reviews, audits, and benchmarking against industry best practices, companies can identify areas for improvement and implement corrective actions. Fostering a culture of innovation and continuous learning within the organization can lead to creative solutions and process innovations that drive better performance in reverse logistics.
Companies can optimize their reverse logistics processes, cut costs, and ultimately improve the customer experience by adopting a comprehensive strategy that includes data analytics, collaboration, clear communication, and continuous improvement techniques.
What are the 5 R’s of reverse logistics?
The fundamental ideas that direct the efficient handling of product returns and the whole reverse logistics process are known as the “5 R’s of reverse logistics.” Return, Recall, Repair, Resell, and Recycle are these guiding concepts.
1. Return: Taking care of consumer goods returns is the initial stage in the reverse logistics process. This entails establishing unambiguous return guidelines, offering simple return alternatives, and processing returned goods quickly to decide what to do next.
2. Recall: Businesses need to have a strong recall procedure in place in order to promptly take the product out of distribution and handle any possible hazards to customers in the event that a recall is necessary owing to safety concerns or flaws.
3. Repair: In order to bring items that can be mended and resold back to marketable condition, a comprehensive repair procedure should be carried out. This might entail quality control inspections, diagnostics, and refurbishment to make sure the product satisfies the requirements.
4. Resell: Products may be put back on the market for sale after being fixed or judged appropriate for resale. Businesses should have plans in place to make the most out of returned goods, such selling them for less or combining them with other items to make them seem more appealing.
5. Recycle: The last phase in the reverse logistics process is recycling for goods that can’t be fixed or resold. This entails discarding the product in an appropriate manner and recovering any precious elements for use in other products or industries.
By following the 5 R’s of reverse logistics, companies can effectively manage product returns, reduce waste, and maximize the value of returned products, ultimately improving their overall reverse logistics operations.
What are the 7 R’s of reverse logistics?
A thorough method for handling product returns and streamlining the reverse logistics procedure is included in the seven Rs of reverse logistics. The extra R’s are Reduce and Reuse in addition to Return, Recall, Repair, Resell, and Recycle.
6. Reduce: In reverse logistics, the idea of reducing focuses on decreasing the quantity of returns and, where feasible, avoiding needless returns. Businesses may lower the amount of returns and related expenses by increasing customer service, offering accurate product information, and improving product quality.
7. Reuse: Reusing components or returned goods can help reduce waste and increase the value of returned goods. Companies might look for ways to extend the lifetime of returned goods and lessen their environmental effect by refurbishing, repurposing, or repackaging them for future sales.
Businesses may increase the efficiency of their reverse logistics operations overall, cut waste, and strengthen their sustainability initiatives by integrating the concepts of Reduce and Reuse into the Five R’s of reverse logistics.
Hope this article was helpful for more check out our previous blog post by clicking here